AWS for Industries
Building software-defined vehicles with AWS and NXP
The automotive industry is going through a major transformation to address the growing demand for connected, electric, and autonomous vehicles. This transformation opens up new opportunities and benefits for automakers and automotive suppliers. Customers receive new features from over-the-air (OTA) updates that facilitate functionality in software without ever visiting a service station. Automotive manufacturers can continue to improve their vehicles over time and offer new business models, such as facilitating on-demand features and subscription services.
To build connected, electric, and autonomous vehicles, automakers are adopting software-defined vehicle architecture to consolidate vehicle functionality, such as infotainment, vehicle subsystems, and human-interface applications, into updatable software applications. Software-defined vehicles require a cloud solution with scalable data ingestion and connectivity combined with a robust in-vehicle architecture for data collection and edge processing. In this blog post, we will examine how Amazon Web Services (AWS) and NXP Semiconductors accelerate this transformation for the automotive industry by providing fully integrated hardware-to-cloud solutions.
Overview of solution
To address the needs of automakers building software-defined vehicles, hardware and cloud providers must partner closely to have tightly integrated services. Prebuilt integrations take care of the connectivity and security challenges that developers face when building connected software-defined vehicles so that they can focus on creating great driver experiences and robust in-vehicle software. AWS and NXP have collaborated to simplify vehicle architecture, process and ingest a growing amount of data from vehicles, and provide sample applications for developers to bootstrap their software development.
Simplify vehicle architecture
Hardware-centric vehicles integrate dozens of electronic control units (ECUs) to implement subsystems in the vehicle. New features are added to vehicles by introducing new ECUs with their own software and closed system.
Software-defined vehicles use high-performance multicore automotive vehicle gateways that support multiple applications and services simultaneously. Instead of building hardware and software for dozens of ECUs, automakers can now focus on building functionality in software using common hardware solutions.
Vehicle gateways are placed on the vehicle’s network to interact with multiple controller area network (CAN), LIN, and automotive Ethernet interfaces. Due to their centralized location and interface with vehicle data sources, vehicle gateways are ideal to run the edge processing software necessary to extract value from this data.
Figure 1 shows the simplification of vehicle architecture by moving from a hardware-centric distributed vehicle architecture to a highly centralized software-defined vehicle architecture using service-oriented vehicle gateways. In the hardware-centric vehicle, ECUs operate in isolation. In a software-defined vehicle architecture, a few central service-oriented gateways control domains within the vehicle.
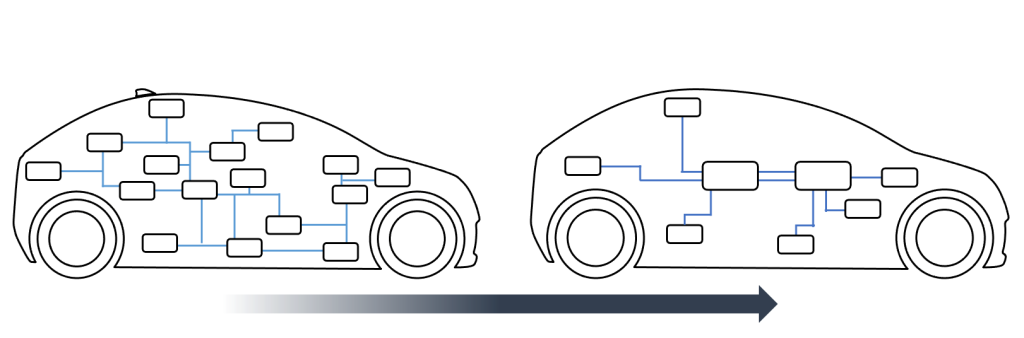
Figure 1. Simplify vehicle architecture by transitioning from a hardware-centric vehicle to a software-defined vehicle with service-oriented gateways.
The NXP S32G is an in-vehicle gateway and network processor that combines multicore Arm Cortex-M7 processors and Cortex-A53 processors with network and security acceleration and is designed to support up to ASIL-D functional safety applications.
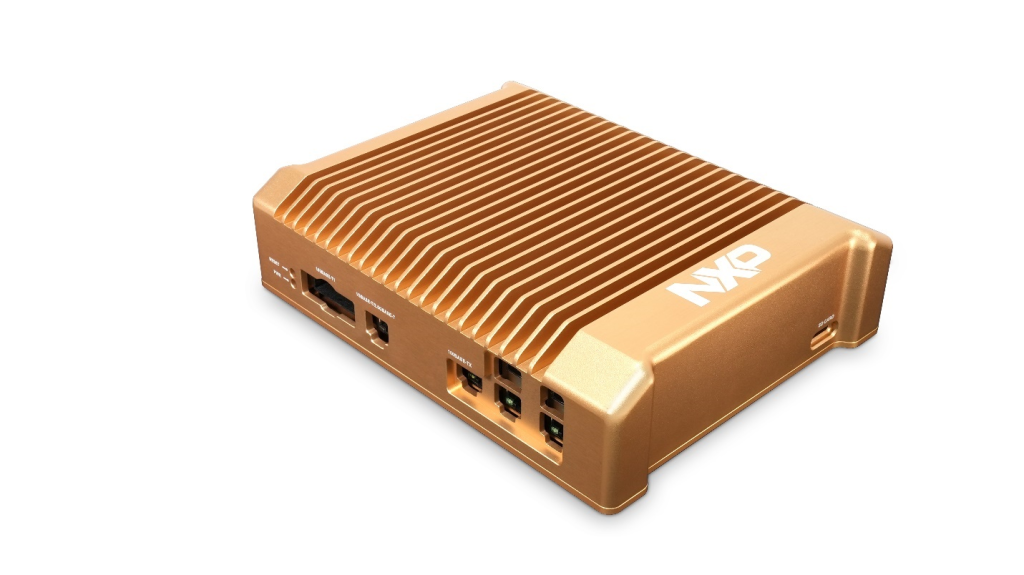
Figure 2. NXP GoldBox S32G reference platform (source: NXP GoldBox website)
Ingest data from the vehicle
The volume of data from sources such as sensors, lidar, advanced driver assistance systems (ADAS), and interfaces continues to increase despite the reduction in the number of processors in a vehicle. According to a McKinsey & Company study, a modern vehicle can produce up to 25 GB of data per hour, and as new technologies and automation are introduced, this volume of data will increase. Data is transmitted throughout the vehicle in different protocols and formats. This data requires protocol translation and normalization before it can be used in a connected vehicle. Analyzing data at the source facilitates in-vehicle software to make intelligent decisions for rider comfort and create high-quality driver experiences in near real time.
Only data that is needed by a vehicle manufacturer to address a business problem needs to be transmitted to the cloud, but the software-defined vehicle must be flexible enough to allow for new data sources to be ingested on demand. Aggregation, filtering, and analyzing this volume of data near to the source requires high-performance processors and capable software.
AWS provides native services and solutions that facilitate scalable ingestion of vehicle data for automotive manufacturers.
AWS IoT Greengrass is an open-source Internet of Things (IoT) edge runtime and cloud service that helps you build, deploy, and manage applications on connected vehicles over the air. Greengrass runs on in-vehicle gateways to act locally on the data that the vehicle generates, run predictions based on machine learning models, and filter and aggregate vehicle data. Automotive manufacturers use AWS IoT Greengrass to deploy software to software-defined vehicles over the air and provide connectivity to the cloud for data ingestion.
AWS IoT Core is a device gateway and message broker that facilitates scalable data ingestion from vehicles as well as command and control of the vehicle from the cloud. IoT Core is an entry point from which connected vehicles connect to the cloud and exchange messages with downstream services such as databases, machine learning, and analytics services.
AWS IoT FleetWise makes it easy and cost effective for automakers to collect, transform, and transfer vehicle data to the cloud in near real time and use it to build applications with analytics and machine learning that improve vehicle quality, safety, and autonomy. AWS IoT FleetWise allows automakers to select only the data that they need from their fleet of vehicles and collect that data in a defined time window, called a campaign.
AWS solutions such as the Connected Mobility Solution for vehicle fleet management and AWS IoT FleetWise for vehicle data collection are tightly integrated with NXP’s S32G vehicle network processors. The S32G Reference Design Board 2 (RDB2) and S32G GoldBox reference hardware platforms are qualified for AWS IoT Greengrass, which means that they have integrated AWS IoT Greengrass into their board support packages (BSPs) and have passed all related AWS IoT Greengrass tests with IoT Device Tester for AWS IoT Greengrass.
Accelerate the developer experience from edge to cloud
To accelerate the software development of in-vehicle service-oriented gateways, NXP provides a reference software platform called Gold Vehicle Integration Platform (GoldVIP). GoldVIP preintegrates NXP and AWS software into the BSP for the S32G vehicle network processors. Services provided in GoldVIP include support for vehicle networking, in-vehicle services, data analytics, cloud services, OTA updates, virtualization, and security services. Customers that use GoldVIP can focus on rapidly prototyping their applications without spending additional development time porting the necessary software for connected vehicles.
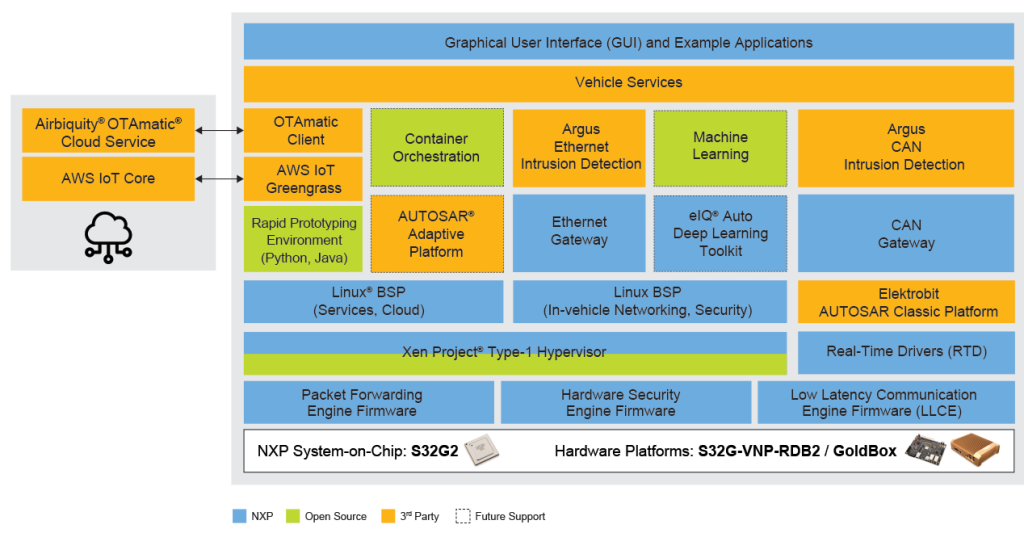
Figure 3. GoldVIP software block diagram and architecture (source: NXP GoldVIP website)
GoldVIP includes out-of-the-box support for the AWS IoT Greengrass edge runtime and connectivity to AWS IoT Core. Two sample applications are provided that showcase this integration. The sample application infrastructure is deployed and configured in the developer’s AWS environment using the AWS Serverless Application Repository (SAR).
The first sample application, Cloud Edge Gateway, collects telemetry data, including virtual central processing unit (vCPU) load on all four Cortex-A cores, network traffic volume, memory usage, and component temperatures from a function of AWS Lambda—a serverless, event-driven compute service that lets you run code for virtually any type of application or backend service without provisioning or managing servers—deployed on AWS IoT Greengrass. These telemetry metrics are published to AWS IoT Core and displayed on an AWS IoT SiteWise Portal dashboard in near real time. Figure 4 showcases the sample application architecture. Figure 5 showcases the AWS IoT SiteWise application dashboard, which demonstrates the overall CPU load used by all applications running on the software-defined vehicle gateway.
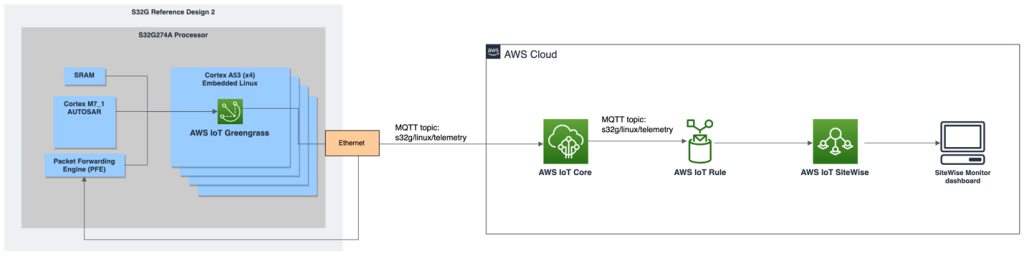
Figure 4. The Cloud Edge Gateway telemetry application architecture

Figure 5. The AWS IoT SiteWise dashboard showing a spike in load on vCPU3 of the S32G
The second example application, SJA1110 Telemetry, uses the SJA1110 Time-Sensitive Network Ethernet switch onboard the reference hardware to show the switch packet performance in near real time. Data is collected from the Arm Cortex-M7 processor running FreeRTOS, published to AWS IoT Core through AWS IoT Greengrass as a client device, and displayed on AWS IoT SiteWise Portal dashboards. Figure 6 showcases the architecture for this application. Figure 7 shows the AWS IoT SiteWise dashboard displaying statistics for all data ingested from the vehicle’s interfaces that is processed by the SJA1110 Ethernet switch.
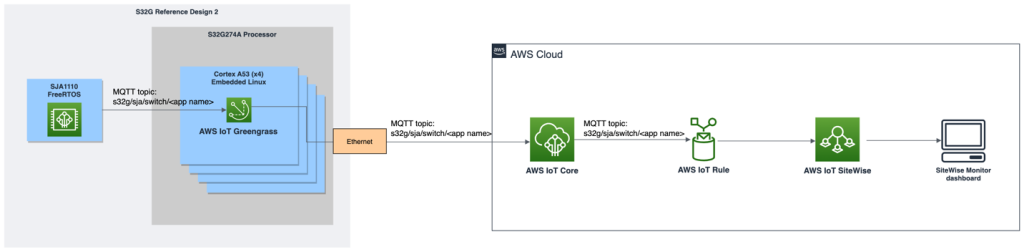
Figure 6. The SJA1110 Switch network performance sample application architecture
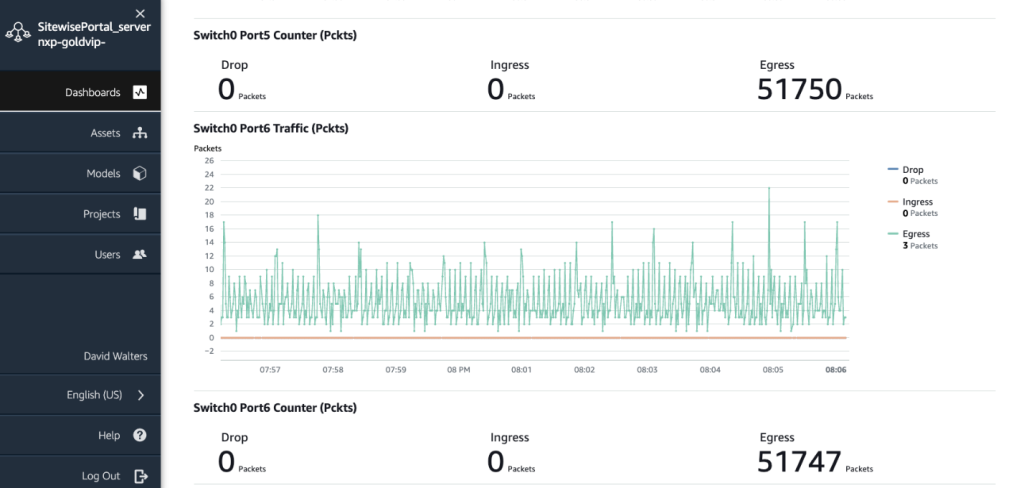
Figure 7. The AWS IoT SiteWise dashboard showing network traffic on Port5 and Port6 of the SJA1110 network switch
The sample applications are provided as references to bootstrap new AWS connected applications using AWS IoT Greengrass and FreeRTOS on the S32G and help developers understand how their applications are performing on the S32G processor and associated hardware peripherals. Developers can see the current memory, CPU usage, and network performance in real time as they deploy and test new applications.
GoldVIP also provides a Yocto Project environment for users to create their own customized GoldVIP builds that can incorporate additional capabilities and new vehicle services. The GoldVIP Yocto Project contains meta-aws recipes for building AWS edge software capabilities to the processor’s Embedded Linux operating system with OpenEmbedded and Yocto Project build frameworks.
To get started using GoldVIP, instructions on how to download the GoldVIP software and deploy the sample application on AWS are available from the NXP GoldVIP website.
Conclusion
NXP and AWS have worked together to create solutions and developer tools to accelerate the transition to connected, autonomous, and electrified vehicles. Software-defined vehicles require robust multicore in-vehicle processors that are located centrally on the vehicle network. AWS device software, such as AWS IoT Greengrass, provides the connectivity and OTA update capabilities to facilitate software-defined vehicles. Scalable cloud infrastructure is needed to provide the backbone for connected vehicle services to ingest and manage the volumes of data generated by vehicles.
Developers that are working on software-defined vehicles face new challenges so that these technology components are seamlessly integrated. GoldVIP provides an out-of-the-box software evaluation solution to run on the NXP S32G and connect securely to the AWS Cloud. Instead of working on tasks such as integrating existing software onto the in-vehicle gateway, developers can now focus on building applications that meet their customers’ expectations.
Further reading: