AWS Internet of Things
Unlock your IoT data and accelerate business growth
Why AWS IoT?
AWS offers Internet of Things (IoT) services and solutions to connect and manage billions of devices. Collect, store, and analyze IoT data for industrial, consumer, commercial, and automotive workloads.
Benefits of AWS IoT
AWS IoT services
Connect your devices and operate them at the edge.
FreeRTOS
AWS IoT Greengrass
Amazon Kinesis Video Streams
AWS IoT ExpressLink
Connectivity and control services
Secure, control, and manage your devices from the cloud.
AWS IoT Core
AWS IoT Device Defender
AWS IoT Device Management
AWS IoT FleetWise
Analytics services
Work with IoT data faster to extract value from your data.
AWS IoT SiteWise

AWS IoT Events

AWS IoT Analytics
AWS IoT TwinMaker
Possibilities with AWS IoT
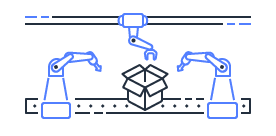
Optimize industrial operations
Create rich and scalable industrial IoT applications to remotely monitor operations, improve quality, and reduce unplanned downtime.
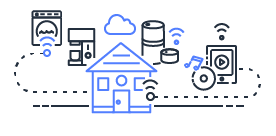
Build differentiated consumer products
Develop connected consumer applications for home automation, home security and monitoring, and home networking.
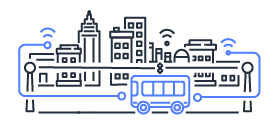
Reinvent smart buildings and cities
Build commercial IoT applications that solve challenges in infrastructure, health, and the environment.
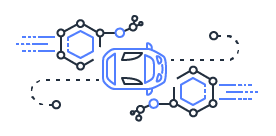
Transform mobility
Deliver IoT applications that gather, process, analyze, and act on connected vehicle data, without having to manage any infrastructure.
Volkswagen Group
We will continue to strengthen production as a key competitive factor for the Volkswagen Group. Our strategic collaboration with AWS will lay the foundation.
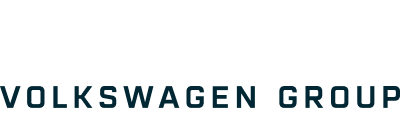
iRobot
Traffic spiked by at least 20 times, but because of the simple scalability of a serverless AWS architecture, it was a nonevent. With a traditional architecture, it would have been all hands on deck.
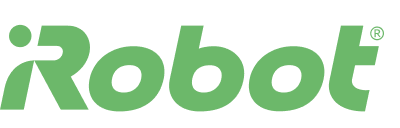
Carrier
Through this collaboration with AWS, we are developing a uniquely powerful ecosystem to give our customers greater flexibility, visibility, and intelligence across the cold chain.
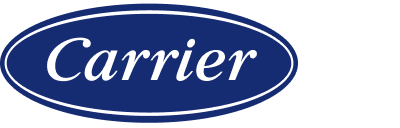