生産ラインの長時間停止によるコストを抑制することができました。
自動車のトランスミッションで世界 1 位※、カーナビゲーションで世界 3 位※のシェアを誇るアイシン・エィ・ダブリュ株式会社。生産性のさらなる向上に向けて、生産システムのデジタル化に取り組む同社は、ブレインズテクノロジー株式会社の支援を受け、エッジコンピューティングを実現する AWS Greengrass とサーバーレスアーキテクチャなどを用いた生産ラインの状態監視システムを構築しました。わずか 1 週間でモデルを構築し、運用開始から 2 週間ほどで “いつもと違う” 状態を検出。生産ラインの長期停止リスクを回避することに成功しています。
※2018 年同社調べ
「品質至上」の経営理念のもと、徹底した品質と先進性にこだわり、常に世界初の商品を世に送り出してきたアイシン・エィ・ダブリュ。長年かけて培ってきたトランスミッションの電子制御技術や駆動用モーター技術、カーナビゲーションの地図情報技術などをベースに電動化、自動運転支援など次世代に向けた先進技術の開発に取り組んでいます。
主力製品であるオートマチックトランスミッション(AT)の生産拠点は国内 5 ヶ所、海外 7 ヶ所にあり、生産ラインには素材の成形、加工、組立、検査、出庫など工程に応じた生産設備を約 2 万台配備しています。それらは厳しい社内基準によって標準化され、高品質のものづくりを支える基盤となっています。
同社は 2016 年に生技開発部内に『生産システム革新グループ』を新設し、業務全体の高度化を推進することにしました。グループ内でさまざまな施策を進める中、新たに取り組んだのがデジタル技術を使ったインダストリアル IoT です。「世界中で IoT や AI を活用した生産革命が起きている中、競争力の強化に向けて先進的な IT 生産システムの開発にチャレンジすることにしました。」と語るのは生産システム革新グループグループマネージャーの佐藤雅則氏です。
同社は生産設備から出力される膨大なデータを活用した状態監視基盤の構築を検討。第 1 ステップとして、組立作業や設備セッティングなど、人に依存する検査過程の要素を自動化することにしました。
「生産ラインの中には人が関与する工程があり、いつ、どこで、どのような変化が起きているかを捉えています。状態監視の部分を IoT や AI を使って自動化、可視化することで省力化を図り、生産性を高めることが目的です。」(佐藤氏)
同社は、バックエンドのサーバー部分で大量の設備データを分析し、作成した学習モデルを設備に設置したエッジデバイスに配信するモデルを考案。第 1 ステップとして、2016 年 3 月に機械学習の基盤をオンプレミス環境上に構築し、エッジ部分に汎用 PC を用いて異常状態を検出する PoC を実施しました。そこでの成果を踏まえ、本格的な分析基盤では製造工程におけるデータの蓄積と機械学習によるモデル作成をクラウド環境で実施し、エッジ部分には専用デバイスを用いたエッジコンピューティングを実装することにしました。生技開発部生産システム革新グループ 担当員の松下誠氏は次のように語ります。
「全社展開を考慮すると、生産拠点間の統一管理ができ、複雑な設計なしに展開ができなければなりません。さらにどの工程でも使用が可能で、専門家以外でも簡単に分析できることも求められます。これらの要素にコストを加味すると、必然的にクラウド+エッジコンピューティングの組み合わせとなりました。」
パートナーの選定において、複数の候補を検討した中から機械学習を活用したデータ分析に実績があるブレインズテクノロジー株式会社を選定しました。「量産ラインへの迅速な導入を実現するためには、立ち回りが早くチャレンジングな会社とオープンイノベーションを進める必要がありました。その中でアジャイル型開発の提案で迅速な動きを見せてくれたのがブレインズテクノロジーでした。」と佐藤氏は語ります。
環境構築はスピードを重視してスモールスタートで進めました。設備データを蓄積し、機械学習によるモデル作成を実行する基盤は、AWS 上にブレインズテクノロジーのリアルタイム大規模データ分析基盤『Impulse』を用いて構築。Impulse は、AWS IoT や AWS Lambda、Amazon DynamoDB などのサーバーレスアーキテクチャで構成され、AWS Batch で学習モデルが作成されています。学習したモデルを展開し、生産設備の異常を検知するゲートウェイデバイスにはローカル環境でのデータ処理を可能にする AWS Greengrass を採用しました。
ブレインズテクノロジー 工場長の中澤宣貴氏は「2017 年 9 月に AWS の東京リージョンで AWS Greengrass が提供されることを知り、お客様への提案を決めました。
AWS を採用した理由は、サービスラインアップが充実し、今後もさまざまな機能が提供されることへの期待からです。」と語ります。
本格的な開発は 2018 年 6 月から着手。生産設備から取得した膨大なデータから機械学習のアルゴリズムを作成し、2018 年 8 月から国内工場の量産ラインの 1 ヶ所で本格利用を開始しました。
「アルゴリズムの作成では、現場の作業者の納得感を重視し、機械学習が検出した情報を使ってすぐに手が打てるようにこだわりました。分析基盤がわずか 2 ヶ月で開発ができたのは、2016 年からの経験と技術の蓄積があったからで、アルゴリズムにはこれまでのノウハウが随所に込められています。」(松下氏)
同社は状態監視システムを量産の生産ラインで稼働させてから約 2 週間後、早速 “いつもと違う” 状態を検出し、ラインの長時間停止とそれに伴うコストの発生を回避することができました。検出した結果から不具合が発生した箇所の原因を特定するスピードも早く、コストの抑制につながっているといいます。機械学習が検出した情報に対しても納得感があることから、現場には 1 ヶ月程度で浸透し、積極的に使われるようになっています。
機械学習のモデル構築時間の短縮化も進み、複数のモデル作成や検証が可能になりました。生技開発部 生産システム革新グループの吉田和導氏は「オンプレミス環境での検証では、1 つの学習モデルを作成し、検証を繰り返して高い精度を実現するのに 1 ヶ月ほど要していました。AWS を導入してからはモデル作成と検証が 1 日、2 日で終わります。そのためより多くの設備、より多くの生産ラインのモデル作成が可能になり、ラインへの導入や拠点への展開がスピードアップしています。」と語ります。
クラウドサービスを採用したことで、サーバーの運用負荷もなくなり、生産システム革新グループの人員リソースをデバイスの設置場所の検討や、アルゴリズムの開発などに集中できるようになったことも得られた効果です。
今回開発した状態監視システムは、すでに国内工場で立ち上げる新たな生産ラインへの横展開が進んでおり、今後も既存の生産ラインや海外工場にも展開していく予定です。「設備や工程により必要なものは変わるため、人が関与する部分も残しながら適材適所でシステムを適用し、最善の環境を提供していきます。」と佐藤氏は語ります。
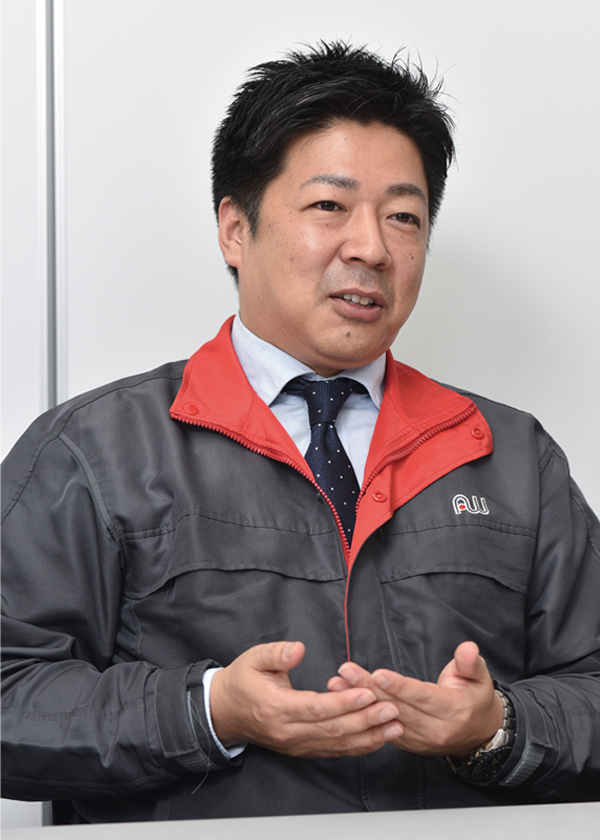
佐藤 雅則 氏
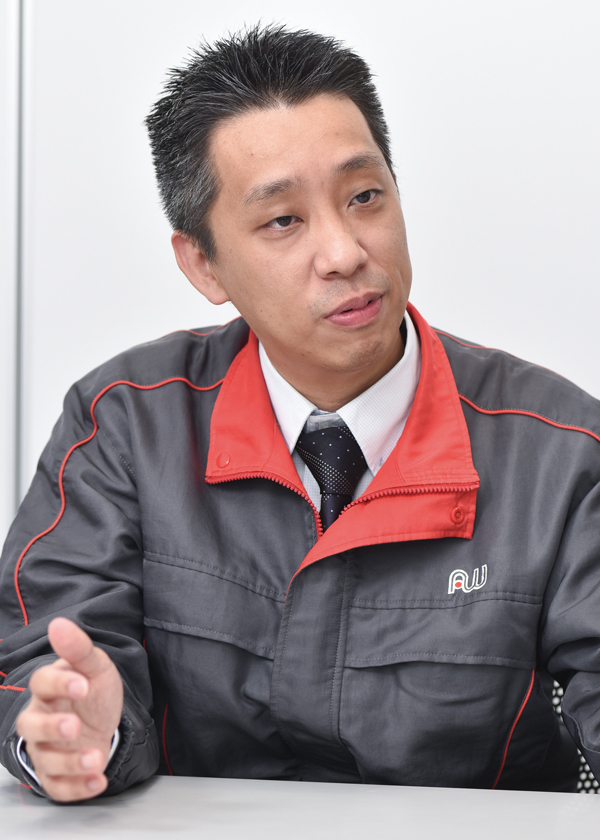
松下 誠 氏
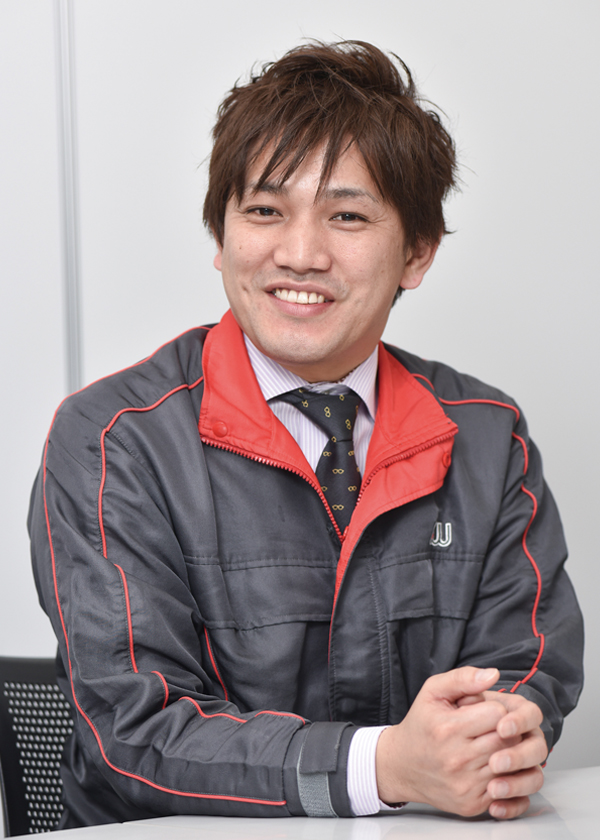
吉田 和導 氏
AWS インダストリアルソフトウェア コンピテンシーパートナー
ブレインズテクノロジー株式会社
プロダクト・ライフサイクルのあらゆる場面で機械学習技術を活用できる、業務特化型機械学習ソリューション「Impulse」を提供している APN テクノロジーパートナー。製造現場で鍛え上げられた「Impulse」は、現場で使える “オートモデリング“ 機能(特許第 6315528 号)を実装し、多くのお客様が実業務で活用されています。
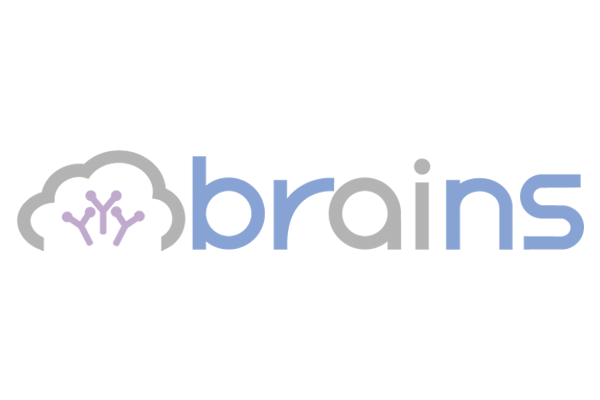