Improve Machine Production Performance with EXOR
Condition Monitoring with EXOR eXware707T IIoT Edge Controller and Gateway
Background
The cost of equipment maintenance not only includes the loss of production but also overhead costs. Unplanned equipment downtime is a top challenge manufacturers attempt to solve to improve machine performance. To do this, manufacturers need to set up effective monitoring and management of equipment with legacy infrastructure and operational technology. This means translating multiple fieldbus protocols including PROFINET, EtherCAT, Ethernet/IP, Modbus TCP, and POWERLINK. The next step is taking the data from the edge into the cloud for time-series analysis to detect anomalies and share results back to maintenance technicians.
Overview
System integrators and machine builders can use the eXware707T IIoT Edge Controller and Gateway to connect to over 200 different fieldbus protocols and interface with operating technology and industrial machinery by using the EXOR JMobile software. Together with AWS IoT Greengrass, the gateway provides a complete intelligent field gateway solution with connection to AWS IoT Core. This dramatically reduces time for deployment with limited interruption to production. The solution also provides an easy to use control application in the cloud or at the edge.
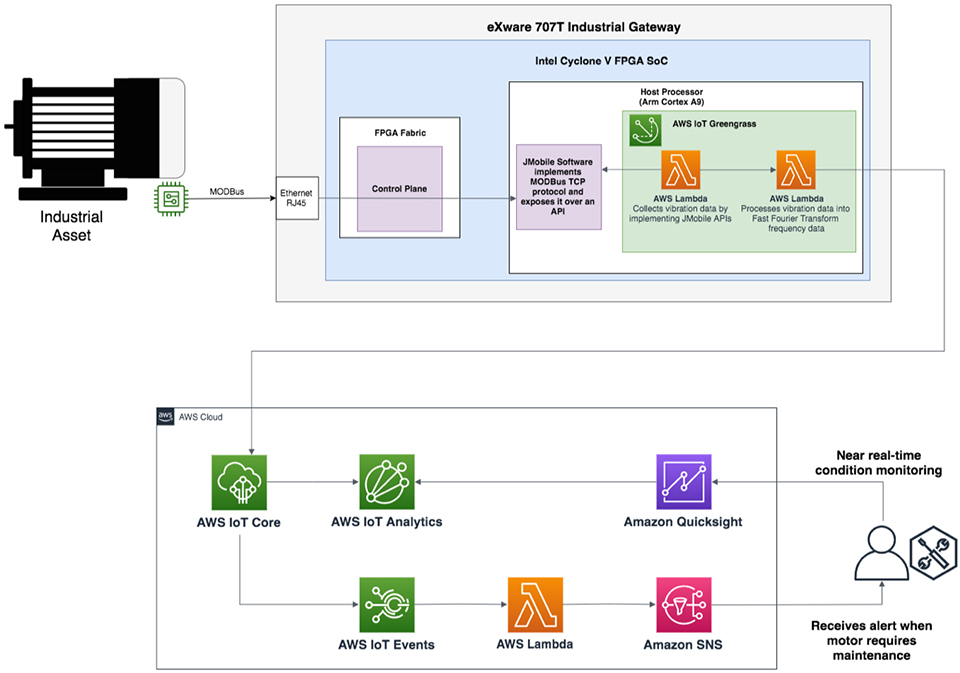
Benefits
The software and hardware architecture of the eXware707T easily collects, processes, and transforms manufacturing equipment data.
- Reduced time to deployment - With the easy to use configuration tool, it is possible to connect a machine in 10 minutes.
- Scale easily - Plug in modules for system expansion, interfacing to sensors for temperature, pressure, vibration, etc.
- Improve Security - eXware707T provides separation between IT/OT network through built in firewall features.
- Native Integration with AWS - Integration with AWS IoT Greengrass opens up scalability and performance by moving the device control to the cloud using AWS tools.
Features
200+ brownfield PLCs protocols
The host processor is used for fieldbus protocol processing using EXOR’s JMobile software, which supports 200+ fieldbus protocols, to connect industrial endpoints to the cloud.
OPC-UA over TSN Switch
TSN enables deterministic latency in local area network communication. With TSN, the edge device can cooperate with other devices on the network to perform real-time tasks. For example, an industrial programmable computer (IPC) can be used to synchronize multiple robot arms on a TSN, ensuring timely delivery of control messages from the IPC to the robot arms.