meaning the costs of extended production line downtime were avoided.
Based on the management philosophy of “quality first,” AISIN AW has continually introduced world-first products with a thorough commitment to quality and innovation. The company is working on the development of advanced technologies for the next generation, including those for electric vehicles and automatic driving assistance, based on the electronic transmission control, drive motor, and car navigation map information technologies it has cultivated over many years.
AISIN AW has five production facilities in Japan and seven overseas for automatic transmissions, its main product, and there are around 20,000 pieces of production equipment on those production lines for processes including material molding, machining, assembly, inspection, and shipping. These are standardized based on strict internal standards, serving as the foundation that supports high-quality manufacturing.
In 2016, the company established a new Production System Innovation Group within its Production Engineering and Development Department to promote enhancement of overall operations. While various measures were being promoted within the group, attention was turned to industrial IoT utilizing digital technology. “As the global IoT and AI-led revolution in production unfolds, we decided to take up the challenge of developing an advanced IT production system to increase our competitiveness,” says Masanori Sato, Group Manager of the Production System Innovation Group.
The company looked into building a status-monitoring platform to utilize the enormous amount of data output from its production equipment. The first step was to automate the elements in the inspection process that depended on manual tasks, including assembly work and equipment setup.
"There are processes on the production line that involve humans, and they keep track of what kinds of changes take place where and when. The purpose of automating and visualizing this status monitoring using IoT and AI is to save labor and improve productivity." says Sato.
A large volume of equipment data is analyzed by a back-end server, and the company devised a model whereby a learning model is distributed to edge devices installed on the equipment. The first step was to build a machine learning platform in an on-premises environment in March 2016, and proof-of-concept was carried out using a general-purpose PC to detect abnormal conditions. Based on those results, in the full-scale analysis platform, a model is created in the cloud environment using data accumulated in the manufacturing processes and machine learning, and edge computing is implemented using a special device. Makoto Matsushita, the person in charge in the Production System Innovation Group, explained.
“Thinking about company-wide roll-out, uniform management has to be possible across production facilities, and it has to be rolled out without a complicated design. You also have to be able to use it in all processes, and even non-specialists need to be able to easily perform analyses. When adding the costs for these elements, we inevitably landed on a combination of cloud and edge computing. ”
The company selected Brains Technology, Inc. as its partner from among several candidates because they had a track record in data analysis utilizing machine learning. Sato recalls, “To quickly introduce this on our mass production lines, it was necessary to work on open innovation together with an astute and enterprising company. It was Brains Technology that demonstrated quick action with agile development. ” says Sato.
Emphasis was placed on building the environment quickly, starting small. The platform for accumulating equipment data and creating models with machine learning was built on AWS using Brains Technology’s large-scale, real-time data analysis platform called “Impulse.” Impulse is comprised of serverless architecture, including AWS IoT, AWS Lambda, and Amazon DynamoDB. Learning models are created by AWS Batch. AWS Greengrass, which enables data processing in a local environment, was adopted as the gateway device for rolling out learned models and detecting abnormalities in production equipment.
Brains Technology Plant Manager Nobutaka Nakazawa says, “I learned that AWS Greengrass was going to be provided in the AWS Tokyo region in September 2017 and decided to propose it to our customer. The reason we adopted AWS was that it has an extensive lineup of services, and we expect that they will continue to provide various features.”
Full-scale development began in June 2018. A machine learning algorithm was created from the enormous amount of data from the production equipment, and full-scale use was launched in one part of the mass production line at a domestic plant in August 2018.
"When creating the algorithm, emphasis was placed on making sure it was satisfactory to workers on the front lines, and we focused on making sure they could use the information detected by machine learning to take quick action. We were able to develop the analysis platform in just two months thanks to the experience and skills accumulated since 2016, and our know-how has been incorporated throughout the algorithm." said Matsushita.
About two weeks after going live with the status-monitoring system on the mass production line, the company was able to avoid costs associated with extended downtime when the system detected abnormal conditions. Based on the results, they were able to quickly identify the location where the problem occurred, which led to cost savings. Because of the satisfactory nature of the information detected by machine learning, the system took root throughout the front lines in about a month, and is now used actively.
The time required to build machine learning models has also been reduced, and now multiple models can be created and tested. Katsudo Yoshida of the Production System Innovation Group says, “It used to take around a month to create a learning model and achieve a high level of accuracy through repeated testing in the on-premises environment. Since going with AWS, model creation and testing is completed in one or two days. That has enabled us to create models for more equipment and more production lines, and we can introduce them on other lines and roll them out to other facilities faster.”
Adopting cloud services also eliminated the burden of server operations, and the human resources of the Production System Innovation Group were able to focus on looking into where to install devices and developing algorithms.
The status-monitoring system that was developed has already been rolled out to new production lines launched at domestic plants, and it will continue being rolled out to existing production lines and overseas plants. Sato says, “The requirements vary depending on the equipment and process, so we will apply the system where needed while maintaining some human involvement to provide the optimal environment.”
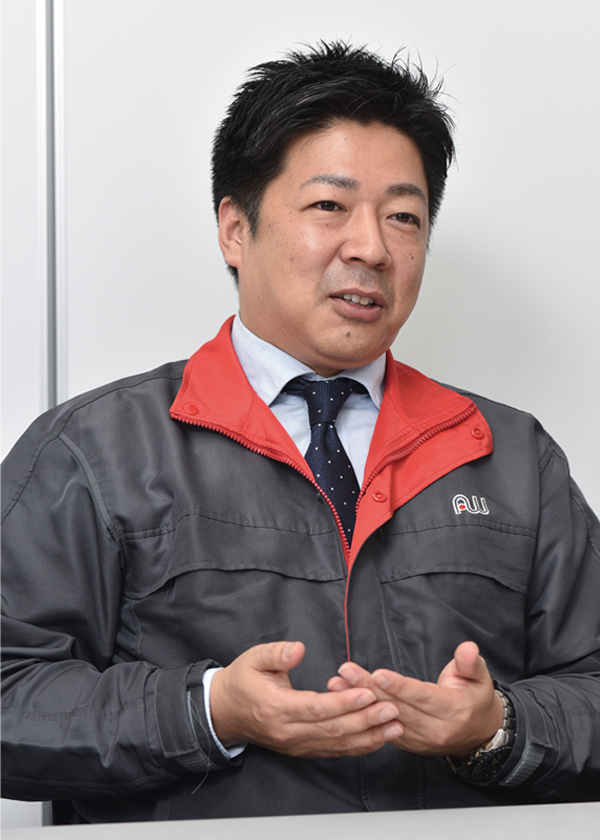
Masanori Sato
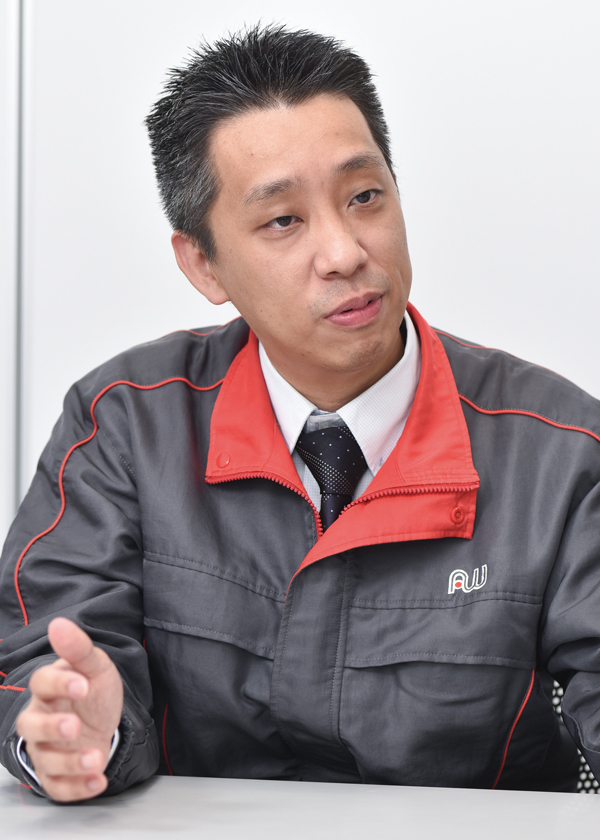
Makoto Matsushita
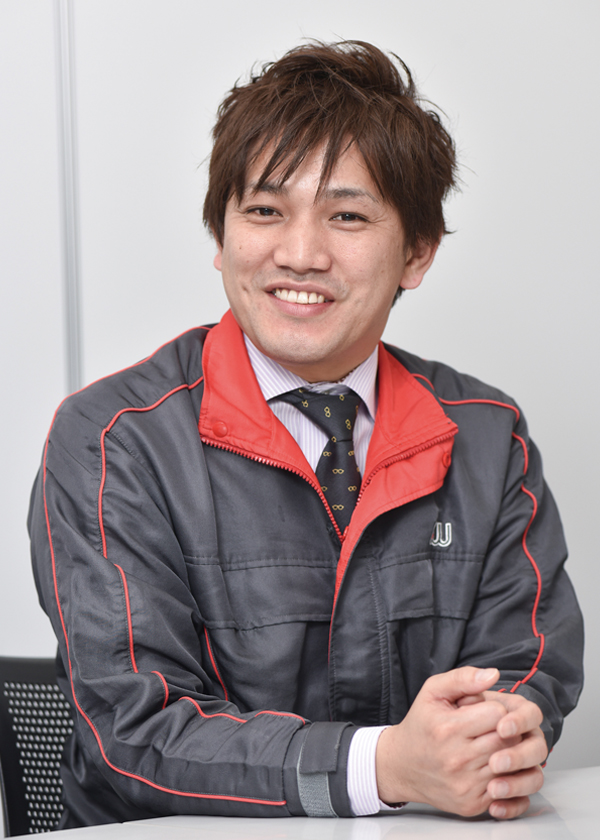
Katsudo Yoshida
AWS Industrial Software Competency Partner
Brains Technology, Inc.
APN Technology Partner providing “Impulse,” an operation-specific machine learning solution that allows machine learning technology to be used in various parts of the product life cycle. Refined at manufacturing sites, Impulse is equipped with an auto-modeling function (Patent No. 6315528) that can be used at the work site and is used by many customers in their actual operations.
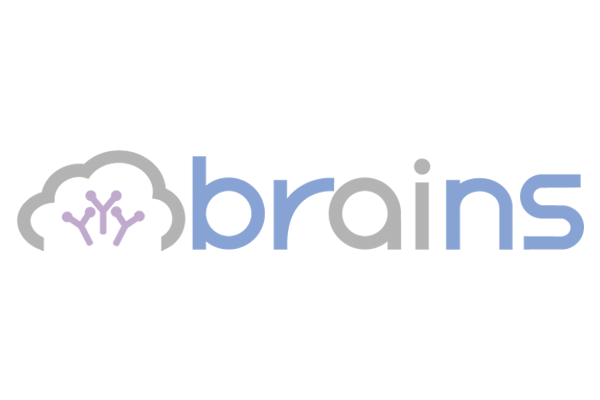