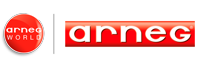
Arneg Predicts Customer Maintenance Needs Worldwide Using Amazon Forecast and Amazon SageMaker
2020
Arneg SpA (Arneg) needed to evolve beyond a reactive customer service model. The company, a global leader in commercial refrigeration manufacturing, sought a failure-tolerant, scalable solution to improve its existing services and integrate with new services as its offerings expanded. To help the company evolve, Arneg turned to Amazon Web Services (AWS) and developed a predictive maintenance model using its Internet of Things (IoT) infrastructure and Amazon Forecast, a fully managed service that uses machine learning (ML) to deliver highly accurate forecasts. The new system enabled Arneg to predict maintenance needs with more than 80 percent accuracy, greatly reducing refrigeration downtime for the company’s global customers.
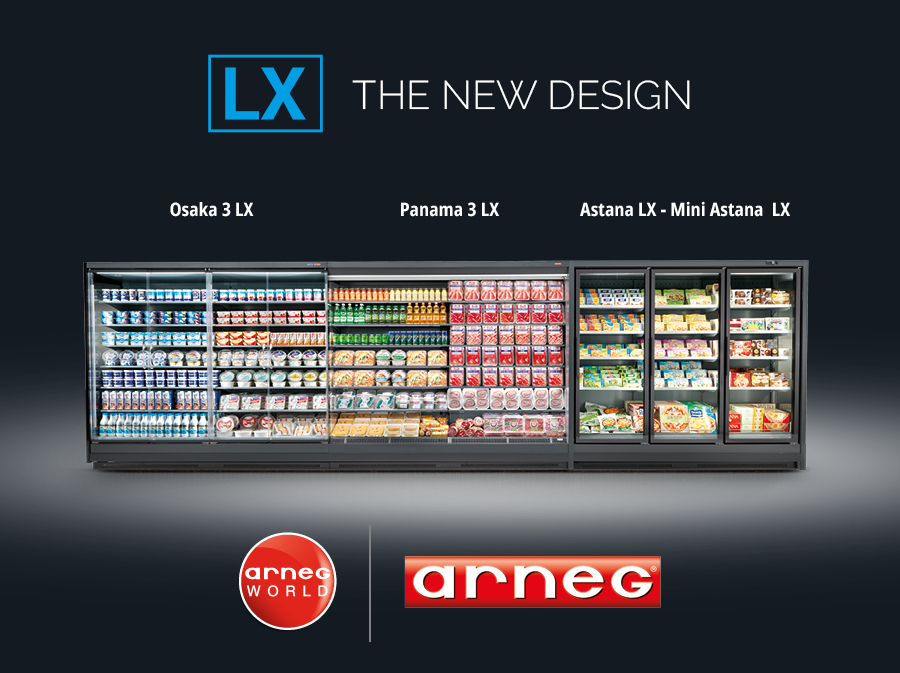

AWS architecture proved to be a great and powerful innovation enabler."
Claudio Canepa
Chief Information Officer, Arneg
Shifting to a Cloud-Based Predictive Model
With a distribution network that spans more than 100 countries, Arneg and its subsidiaries are global manufacturers of freezers and refrigerators for supermarkets and have a strong and recognized positioning in the market. The nature of the business requires the company to respect strict service-level agreements. To facilitate food safety, Arneg must provide around-the-clock customer support worldwide, every day of the year. Arneg previously used its Interactive Remote Information System (IRIS), a locally hosted application, to manage alarms, service calls, and onsite work. With IRIS, refrigerators would send alarms to Arneg when they were malfunctioning—but only when the units could not maintain the strict commercial refrigeration industry standards. “Since assistance is normally only requested when a problem arises, our reaction time needs to be extremely short,” says Arneg service director Davide Zandonà. “This increases our costs and, more importantly, makes the service process less efficient.” Arneg sought to use its existing IoT infrastructure to build a more proactive solution in the cloud. “The development of new projects like predictive maintenance is actually only possible in the cloud,” says Arneg chief information officer Claudio Canepa. “The necessary computing capacity, storage, and organization time cannot be provided on premises.”
The company evaluated multiple global cloud providers and ultimately determined AWS was the best fit. “Our commitment to optimizing and evolving Arneg’s services over time requires the use of easily updatable and upgradable systems,” says Canepa. “Our comparative research identified AWS as the supplier most closely in line with our company’s needs at the time and best able to support future innovations.” Arneg’s first step was developing a proof of concept for the IRIS application on AWS, but the company quickly realized the solution needed to do more than just migrate existing data to the cloud in order to produce tangible benefits. The company identified a need to become cloud optimized, not just cloud hosted, in order to reduce costs, develop its predictive maintenance solution, and continue evolving at scale. Arneg soon realized that AWS microservices enabled it to change and improve existing IRIS functions and to get more benefit from the cloud architecture.
Shortening IoT Creation Timelines to Enable Faster Responses
Arneg’s solution involves collecting data—such as temperatures, energy consumptions, and failures—through IoT devices in freezers and refrigerators and sending that data to the cloud, where it is standardized and homogenized so that it can be processed. Arneg uses Amazon SageMaker and Amazon Forecast for its predictive model. Amazon SageMaker integrates ML components into a single tool set to build, train, and deploy ML models quickly. With its predictive model, Arneg collects 11 million IoT records daily and builds them into models in hours. Previously, building models on this scale took weeks or months.
The predictive model issues a notification before an event is likely to occur, which gives service teams time to monitor the equipment and notify onsite maintenance personnel in advance when necessary. “This solution enables us to provide better quality service by preventing refrigeration unit breakdowns,” says Zandonà. “This also helps optimize the cold chain, improving efficiency and energy savings for retailers while facilitating food safety for consumers.” So far, the predictive maintenance model predicts maintenance needs with 80 percent accuracy—a figure that is poised to improve as the company compiles a large amount of historical data.
Improving Customer Service
Arneg can seamlessly integrate additional services with its solution on AWS. “By optimizing response times and the required maintenance efforts, we have been able to focus more attention on product-service development and on the acquisition of new types of data,” says Zandonà. The company’s next step is to move its customer service contact center to AWS. The ongoing migration process uses Amazon Connect, an omnichannel cloud contact center that provides real-time and historical analytics as well as voice and chat functions.
The migration was driven by a need to improve call times, direct calls based on the data associated with the customer, and reduce time spent identifying, entering, and tracing customer data. “By creating complex workflows in Amazon Connect, it will be possible for us to associate data from suppliers, customers, and points of sale,” says Canepa. “This will help our operators to precompile all the information they need to open a ticket and avoid human errors in data input and flow management.” Once the solution is fully implemented, Arneg can trace requests and data analytics in near real time and create key performance indicators to help monitor and optimize service performance on a continuous basis.
Looking Ahead to Further Innovation on AWS
Looking to switch from a reactive to a preventative service model, Arneg used its IoT infrastructure as well as Amazon SageMaker and Amazon Forecast to develop a predictive model to anticipate its customers’ maintenance needs with more than 80 percent accuracy and prevent breakdowns. Arneg also saw an opportunity to automate and streamline customer service using Amazon Connect—and that’s just the start. “AWS architecture proved to be a great and powerful innovation enabler,” says Canepa. “AWS will enable Arneg to concentrate on the services we see as fundamental for our company and will enable resources normally assigned to infrastructure support, capacity analysis, and the management of complex information technology services to be redirected toward our group’s core business.”
To learn more, visit aws.amazon.com/forecast/.
About Arneg
Arneg is a leading manufacturer of commercial refrigerators. The group’s 20 production companies and 17 international offices drive a global distribution network in over 100 countries.
Benefits of AWS
- Built a predictive maintenance model using ML
- Collects 11 million IoT records daily
- Builds models from IoT records in hours, not days
- Anticipated customer maintenance needs with more than 80% accuracy
- Streamlined customer service
AWS Services Used
Amazon Forecast
Amazon Forecast is a fully managed service that uses machine learning to deliver highly accurate forecasts.
Amazon SageMaker
Amazon SageMaker is a fully managed service that provides every developer and data scientist with the ability to build, train, and deploy machine learning (ML) models quickly.
Amazon Connect
Amazon Connect is an easy to use omnichannel cloud contact center that helps companies provide superior customer service at a lower cost.
Get Started
Companies of all sizes across all industries are transforming their businesses every day using AWS. Contact our experts and start your own AWS Cloud journey today.