Connected Field Work
Day-to-day workflows to manage critical, operational activities are largely still manual - handled with paper, spreadsheets, and person-to-person communication – methods that are long-trusted and accepted, but slow down efficiency, control, and response times. As a result, many factors in the field are at risk, including opex, quality control, field compliance, and HSE.
The Connected Field Work (CFW) solution is a cloud-native offering that provides a centralized, web and mobile-based platform to unify core, operational resources into a single, digital workflow. As a cloud-based solution, CFW can easily scale across multiple operational workflows to fit business needs.
Connected Field Work provides real-time visibility into field-critical activities to improve how personnel track, monitor, and collaborate on operational processes, so job tasks can be completed accurately, efficiently, and safely.
Use Cases
- Work permit and document management
- Field inspections and quality control
- Inventory tracking
- Project tracking
- Maintenance planning, scheduling, execution
- Field safety and risk reporting
Field services management
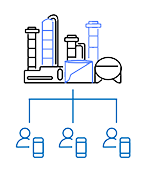
Monitor, track, and collaborate on critical field activities
Unify core, operational resources into a
single, digital workflow
Benefits and Values
- Opex control
- Workforce productivity
- Operational compliance
- HSE risk management
Customer References
Shell with Cumulus Digital Systems
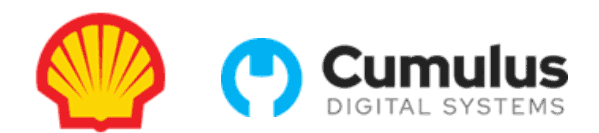
Challenge:
Construction of the Shell Pennsylvania Chemicals Project has beenunderway since 2016. In March 2020, Shell immediately suspended sitework to slow the spread of COVID-19, while progressing approximately 7,000 bolted connections leading up to the temporary shutdown.
Solution:
Shell had previously adopted Cumulus Digital Systems’ Smart Torque System (STS), running on AWS cloud infrastructure, to manage 100k+flanged piping connections. Construction bolt data is digitally saved inreal-time on tablets and uploaded to cloud-hosted database for aggregation and analysis.
Impact:
- 4,500+ connections remotely reviewed, inspected, and signed-off during site shutdown
- Preservation of all bolted connection documentation for efficient restart
- 60% reduction in quality control resources utilized for connection verification and start-up
- 0 reported leaks on start-up
Royal Vopak with OutSystems
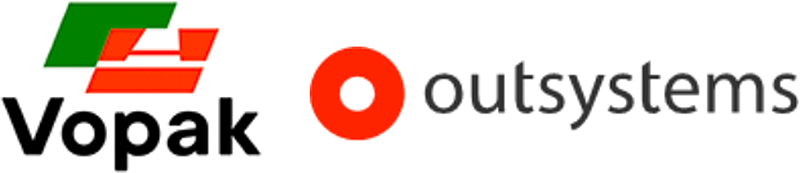
Challenge:
Royal Vopak was replacing its legacy JD Edwards ERP systemand looking for a new terminal management system for improved enhancements and to drive customer-focused innovation. Vopak’s competitive advantage comes from adapting quickly to customer requirements, so the company was looking for an agile approach to serve the market.
Solution:
Vopak adopted OutSystems as an application platform to custom-build its terminal management system (TMS). TMS started in 2016 and has since scaled to go-live at 28 terminals worldwide, as of late 2021. TMS manages customer agreements/contracts, stock movement orders, and order execution of 750+ products.
Impact:
- 4X agility increase vs. historical ERP change management
- 50% less time for terminal workers to complete compliance-related field tasks
- Improved customer experience with real-time tank information access via portal
- Elimination of paper-based procedures with mobile device enablement
How to get started
Step 1 »
Activities
- Security Reviews
- Data Source Strategy
- Process Flow Discovery
- Device Requirements
- Refine Solution Plan
Step 2 »
Activities
- Workflow Design
- Deploy Platform or Software Environment
- Build Application and Iterative Testing
Step 3 »
Activities
- Live Deployment
- Final Testing
- Training Support
Visit the AWS Solutions Library so you can learn how to get started with Connected Field Work and other solutions for the energy industry.