Customer Stories / Automotive / United States
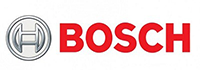
Bosch Creates an Industry-wide Automotive Quality Management Service Framework on AWS
In collaboration with AWS, Bosch Mobility Solutions developed an industry-wide service framework for data-driven quality management. This enables car manufacturers and their suppliers to confidentially and selectively share operational vehicle data for early fault detection.
Data-driven
quality management and collaboration
Confidential exchange
of sensitive data
Acceleration
of early fault detection
Product quality
increased
Cost savings
in defect management
Overview
With 440 subsidiaries in 60 countries, 395,000 employees worldwide, and a revenue of €71.5 billion in 2020, the Bosch Group is a leading international technology and services provider. Its Mobility Solutions division is the largest within the group and one of the leading suppliers to the automotive industry. Bosch is also considered a pioneer in the Internet of Things (IoT), Industry 4.0, and self-driving vehicles.
With its expertise in sensor technology, software, and services, Bosch is able to offer its customers networked and cross-domain solutions from a single source. Bosch is also a key player in digitally networking the German automotive ecosystem, which helps to increase product quality across the ecosystem.
In 2020, Bosch Mobility Solutions launched the development of COVANTO, an industry-wide service framework for data-driven quality management built on Amazon Web Services (AWS). The platform, which has since been completed, is being considered as a solution for Catena-X, the automotive industry's digital framework, which was founded in 2021 to enable Europe-wide data exchanges between car manufacturers and suppliers.
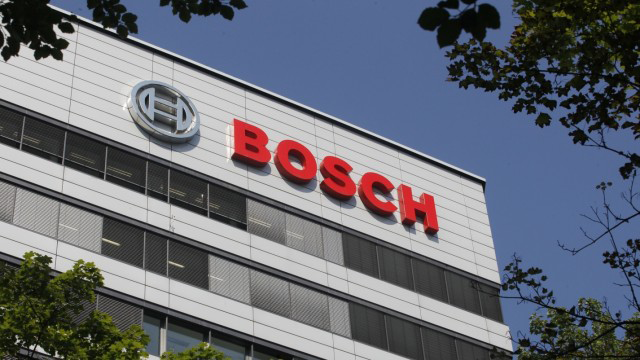
Opportunity
In the automotive industry, it’s critical to identify the causes of problems in new vehicle series as early as possible. When they don’t understand these causes, manufacturers can face high—and sometimes needless—expenses for vehicle repairs during the warranty period. The industry estimates that about 50 percent of all components replaced in auto repair shops are essentially intact.
After a vehicle’s market launch, information about detected malfunctions can be slow to reach companies across the automotive supply chain. Defective parts are usually first sent to car manufacturers for an intial inspection, then to parts suppliers. In some cases, up to 6 months can pass between the time that auto repair shops first notice recurring problems and the time those reports make their way to car manufacturers.
Something often stands in the way of targeted troubleshooting at the supplier level, and that’s the absence of contextual information about how individual components or integrated modules interact with other parts of the vehicle. As modern cars become more complex and the networked functionality of installed components rises, diagnostics need digital development, test, and operating data more than ever. So improving how data is exchanged benefits everyone involved.
The problem is that detailed product data, gathered over years of development work, is often protected by patents held by suppliers or manufacturers. That means that data for quality assurance must be exchanged very selectively—both in terms of which product and operational data is shared and in terms of which companies can access that information. Data also needs to be exchanged quickly, securely, in compliance with governance guidelines, and with as little bureaucratic red tape as possible.
Cooperation with AWS
In 2020, Bosch set out to create a data exchange platform that could meet all of those needs when it launched its Agile Field Quality Management project. Klaus Sekot, head of the project, knew from the start that this required an overarching cloud platform. However, no standard solution on the market met the project’s complex requirements. After speaking with several providers, Bosch chose AWS. “We were impressed that AWS had the foresight to realize that the planned use case of the Agile Field Quality Management project would not remain an isolated case in the long run,” Sekot says.
The next 6 months saw intensive collaboration between AWS and Sekot’s team. “AWS put a lot of effort into understanding the use case in depth,” he says. “We had several workshops with experts from AWS, some of whom had traveled all the way from the US just for this purpose. There was real interest on behalf of AWS to develop the solution.”
After AWS fully defined the use case, the next step was to build a proof of concept (PoC). Bosch Mobility Solutions and AWS built the PoC with services such as Amazon Simple Storage Service (Amazon S3), Amazon Redshift, Amazon Cognito, and Amazon API Gateway. The PoC made it possible for the teams to identify where AWS components needed additional functionality and then develop those while implementing the project. This solution provides line-based access to the database, as well as role-based assignment of access levels to the database.
During implementation, Sekot’s team relied primarily on serverless solutions from AWS. With serverless computing, AWS carries out infrastructure management tasks such as capacity provisioning or patching. This frees up the team’s time to fully concentrate on implementing the required processes and logic.

By merging data, it is possible to significantly accelerate fault detection, in some cases by months.”
Klaus Sekot
Project Director, Field Monitoring and Data Mining, Robert Bosch GmbH
Solution
The service framework that emerged from the collaboration between Bosch Mobility Solutions and AWS is called COVANTO. At the heart of COVANTO is the data access control (DAC) layer, which allows each industry stakeholder to determine precisely which parts of their data should be made available to other stakeholders.
For example, using column-based mapping, a car manufacturer can selectively share operational data from a specific model series. This lets the manufacturer control which data different suppliers can access—a supplier of control units can see operational data for its own units across all vehicles in the series for diagnostic purposes but can’t view control unit data for other vendors. Bosch next plans to implement line-based allocation and access control to make data access even more granular.
To date, several automobile vendors and parts suppliers have pledged to participate in the platform. “Each participant always retains ownership of their data,” Sekot says. “COVANTO does not keep the data in a single large database that everyone can help themselves to. Rather, the data is always stored in the AWS instance of the respective supplier and made temporarily available to other partners individually for service purposes.”
Outcome
COVANTO holds the potential for major impact in data-driven quality management. Car manufacturers and suppliers can save on time and costs by detecting errors and emerging problems early. “By merging data, it is possible to significantly accelerate error detection, by months in some cases,” Sekot says. “This can reduce external error costs by up to 20 percent. The latter can quickly amount to three-digit millions for suppliers in the automotive sector. The effort for troubleshooting in auto repair shops could even be reduced by up to 50 percent.”
Using COVANTO, suppliers will also be able to perform more targeted troubleshooting in the future. The ability to view operational data that’s relevant to their own components often offers suppliers faster visibility into the context of the error they’re investigating. “When suppliers receive a defective part back for analysis, for instance, they often cannot understand why it failed,” Sekot says. “But if they see that—a few weeks before their own part failed—another component that interacts with that part always shows signs of malfunction, they can recognize the pattern and save a lot of valuable time when troubleshooting.”
Such error detection is possible because suppliers have access to the operational data of all components that are functionally connected to their own. At some point, Sekot believes, it would make sense to merge this data with diagnostic data from repair shops so physical error patterns could be matched with data patterns. This could involve monitoring parts to determine whether they continue to fail after they have been modified. In the long term, it might even be possible to digitally map all mechanical and electronic components to enable purely data-driven quality management.
Outlook
Bosch knows that COVANTO’s success depends on the participation of as many manufacturers and suppliers as possible. This means that the platform must be beneficial to everyone participating. Companies must also be able to trust the technology’s data security and integrity. That’s why Bosch plans to publish the source code for the DAC.
In the meantime, COVANTO's operations have been transferred to Caruso GmbH, the automotive industry's joint data services venture for connected vehicles, which will operate the platform as an independent third party. COVANTO is also being evaluated as a solution module for Catena-X, the European automotive industry’s data network. For now, however, the short-term priority is to add new partners, populate the platform with more data, and keep scaling the service framework.
About Robert Bosch GmbH
Through its Mobility Solutions division, Robert Bosch GmbH is one of the leading suppliers to the automotive industry and a pioneer in Internet of Things (IoT), Industry 4.0, and autonomous vehicles technology. The group reported revenues of €71.5 billion in 2020.
AWS Services Used
Amazon S3
Amazon Simple Storage Service (Amazon S3) is an object storage service that offers industry-leading scalability, data availability, security, and performance.
Amazon Redshift
No other data warehouse makes it as easy to gain new insights from all your data. With Redshift, you can query and combine exabytes of structured and semi-structured data across your data warehouse, operational database, and data lake using standard SQL.
Amazon Cognito
Amazon Cognito lets you add user sign-up, sign-in, and access control to your web and mobile apps quickly and easily.
Amazon API Gateway
Amazon API Gateway is a fully managed service that makes it easy for developers to create, publish, maintain, monitor, and secure APIs at any scale.
More Automotive Customer Stories
Get Started
Organizations of all sizes across all industries are transforming their businesses and delivering on their missions every day using AWS. Contact our experts and start your own AWS journey today.