Georgia-Pacific Optimizes Processes, Saves Millions of Dollars Yearly Using AWS
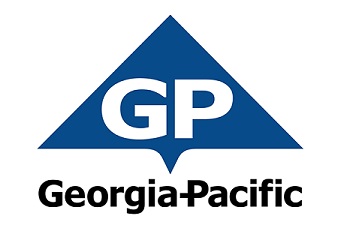
Hundreds of paper and tissue parent rolls are produced every day at Georgia-Pacific manufacturing facilities across North America. Paper production is a delicate and complex operation, during which tears or breaks can happen while manufacturing the parent rolls, and when converting the massive parent rolls into consumer-ready bath or tissue products. If tears or breaks occur frequently, it leads to paper machine and converting-line downtime that can cost Georgia-Pacific millions of dollars per year per line—a number that could be significant given that the company has more than 150 converting lines. “It’s essential that we maintain high machine uptime, and we can only do that if we have good insight into why rolls are likely to break,” says Steve Bakalar, the company’s vice president of IT/digital transformation.
Getting valuable insight, though, was a challenge because the organization relied on disparate sources to collect and analyze data on material quality, moisture content, temperature, machine calibration, and other features. In addition, a small team of site-specific experts hold the knowledge about each site’s unique machinery and processes. “Many of these experts are retiring soon—and taking their knowledge with them,” Bakalar says. To address its need for new data insights and less complex data collection, Georgia-Pacific sought to move to an advanced analytics approach enabled by an operations data lake. “We needed to improve our ability to serve our markets through end-to-end process optimization and improved asset health,” says Bakalar. “We also had to find a way to predict asset failure 60-90 days ahead of time, because we wanted to eliminate unplanned downtime that could negatively impact operations and lead to lost revenue.”
“We are using AWS data-analysis technologies to predict … precisely how fast converting lines should run to avoid tearing. By reducing paper tears, we have increased profits by millions of dollars for one production line.”
Steve Bakalar, Vice President of IT/Digital Transformation, Georgia-Pacific
-
About Georgia-Pacific
-
Benefits of AWS
-
AWS Services Used
-
About Georgia-Pacific
-
Georgia-Pacific, owned by Koch Industries, is an American wood products, pulp, and paper company based in Atlanta, Georgia. The organization is one of the world’s largest manufacturers and distributors of pulp, towel and tissue paper and dispensers, packaging, and wood and gypsum building products.
Optimizing Production and Asset Optimization at Georgia-Pacific with AWS -
Benefits of AWS
-
- Increases profits by millions by optimizing processes
- Predicts equipment failure 60-90 days in advance, reducing unplanned downtime
- Runs more production lines in a predictable manner, better optimizing human and capital resources
- Produces highest-quality products at fastest possible rates
- Increases profits by millions by optimizing processes
-
AWS Services Used
Creating a Cloud-Based Advanced Analytics Solution
To accomplish its goals, Georgia-Pacific chose to create a new analytics solution based in the Amazon Web Services (AWS) Cloud. “We were already in the process of migrating some internal systems to AWS and closing several data centers,” says Bakalar. “We knew AWS could support our data-analytics requirements.” In the first six months, Georgia-Pacific transferred about 50 TB of production data—more than 500 billion records—from hundreds of large, complex manufacturing and converting-process machines. The company uses Amazon Kinesis to stream real-time data from manufacturing equipment to a central data lake based on Amazon Simple Storage Service (Amazon S3), allowing it to efficiently ingest and analyze structured and unstructured data at scale.
Georgia-Pacific knew it could learn from its structured and unstructured data, but the company lacked a cost-effective storage mechanism to ingest, transform, house, and analyze this data.
Georgia-Pacific uses Amazon Elastic MapReduce (Amazon EMR) to transform the data before delivering it in a structured fashion to data analysts through Amazon Redshift. The analysts use Amazon Athena on top of Amazon S3 to query the raw data, which includes information on pulping mechanisms, paper machines, converting lines, vibration trends, throughput, and paper quality.
Georgia-Pacific also uses Amazon SageMaker, an AWS machine-learning (ML) solution, to build, train, and deploy ML models at scale. Using ML models built with raw production data, Amazon SageMaker provides real-time feedback to machine operators regarding optimum machine speeds and other adjustable variables, enabling less experienced operators to detect breaks earlier and maintain quality.
Increasing Profits by Millions by Optimizing Critical Processes
Using its AWS-based advanced analytics solution, Georgia-Pacific optimized key manufacturing processes in many of its facilities. For example, for one converting line, the company eliminated 40 percent of parent-roll tears during the converting process. “We are using AWS data-analysis technologies to predict—based on the quality of a parent paper roll—precisely how fast converting lines should run to avoid tearing,” says Bakalar. “By reducing paper tears, we have increased profits by millions of dollars for one production line. There are 150 lines that could benefit from these optimized processes, so this is a multimillion-dollar opportunity for us.”
At one of Georgia-Pacific’s Oriented Strand Board (OSB) facilities, the organization has seen a 30 percent reduction in waste associated with the chipping process and millions of dollars in increased annual profits.
In addition, at a large paper mill, Georgia-Pacific has optimized a recyclable chemical-recovery process used in making pulp. “We have been able to reduce chemical consumption, and that helps us consume fewer resources while improving overall production yields,” says Bakalar.
These successes are being rapidly scaled across a network of similar facilities.
For selected assets, Georgia-Pacific can now predict equipment failure 60-90 days in advance, so it can reduce unplanned downtime. “We have better, up-to-date data about the performance of machinery throughout all our facilities,” says Bakalar. “This means we can plan equipment downtime, which improves asset utilization and paper mill safety and helps us avoid lost revenue from unscheduled production stoppages.”
Maximizing Plant Resources
In addition to the benefits to its operations, Georgia-Pacific is reducing its reliance on a small number of experts for knowledge about equipment and manufacturing processes. Instead, the company formed a Collaboration and Support Center, augmenting site-specific subject-matter experts with centralized support that promotes technology-enabled decision making.
“AWS enables us to source, store, enrich, and deliver data in a centralized way, which we couldn’t do previously,” says Bakalar. “Using this new model, we believe we can run more production lines in a more predictable manner. As a result, we can leverage our talent pool much more efficiently across our entire organization. Using AWS, we can ensure the highest quality product running at the fastest possible rate, so we can best serve our customers.”