Overview
What’s a Factory Modernisation Assessment?
- A high-level assessment of factory processes and management applications.
- Actionable report highlighting current gaps and sharing uplift paths and high-level remediation roadmaps.
What’s Involved?
Factory walk through with an experienced practitioner, carefully analysing the current state of the factory’s IT, current challenges and requirements, to then provide recommendations to close potential gaps. Learn how the biggest headaches on the factory floor can be solved using modern Cloud technology.
What are the Business Outcomes?
- A tailored report highlighting possible uplift paths to improving operating margin and factory productivity, while increasing quality, safety, and sustainability.
- Benchmark assessment against best-in-class operators.
- Modernisation Roadmap, working the highest priority use cases backwards to actionable initiatives.
- Learn how AWS' wide range of Industrial services, such as AWS Supply Chain, AWS IoT SiteWise and Amazon Lookout for Equipment, can be deployed easily to achieve rapid business results.
What’s Assessed?
- Manufacturing Resource Planning (MRP).
- Enterprise Resource Planning (ERP).
- Overall Equipment Effectiveness (OEE).
- Programmable Logic Controller (PLC).
- Supervisory Control & Data Acquisition (SCADA).
- Manufacturing Execution System (MES).
- Overall Throughput Effectiveness (OTE).
- Data Historians.
- Other electrical/electronic systems.
Who is it Good for?
Factory headcount: 15+
Businesses that:
- Are experiencing disconnect between factory floor IT and corporate IT systems.
- Want to have factory floor automation and integration.
- Want to leverage factory system data but don’t know where to start.
- Are implementing new factory systems/technology.
Typical use cases:
- Replacing older technology.
- Recommending best-fit modern technology.
- Improving process efficiency using IT.
- Improving end-to-end traceability.
- Trialing modern technology such as IoT, advanced analytics and AI.
What are the Steps?
- Questionnaire to establish factory profile (e.g., existing technology, customer requirements).
- Comprehensive, on-site factory walkthrough and workshops: ½ day.
- A business-friendly, PowerPoint assessment and roadmap report created within 1 week - based on Clevvi’s Factory Modernisation Framework - and socialised with key business stakeholders.
- Client feedback and refine.
Average engagement time: 2 weeks.
Who should be Involved?
The most successful engagements involve a wide range of business stakeholders. Examples of who can participate:
Corporate IT:
- CIO/CTO/CISO.
- Infrastructure Engineers.
- Software Developers.
- DBAs.
Factory IT:
- Corporate Electricians.
- Instrumentation Specialists.
- Automation Specialists.
- Maintenance Engineers & Supervisors.
Business Stakeholders:
- COO.
- Production Floor Managers.
- Safety Officers.
- Quality Assurance Managers.
- Compliance Assurers.
- Sustainability Officers.
Why Clevvi?
- More than two decades of experience in factory IT automation within ANZ.
- More than 40 factory modernisation engagements.
- In-depth, specialised skills to address 24x7 operational factory business challenges.
- Vast domain knowledge of food & beverage and manufacturing industries’ business models.
Highlights
- "The guys from Clevvi have added value that we would not have been able to obtain without them. Their hands-on knowledge of manufacturing automation and traceability experience was very impressive.“
- "Our Clevvi factory modernisation engagement helped us save over A$ 1M per year in labour optimisation."
- "Clevvi's ability to talk the language of our operations team got them really engaged and facilitated alignment with our technologists that we've never seen before."
Details
Unlock automation with AI agent solutions
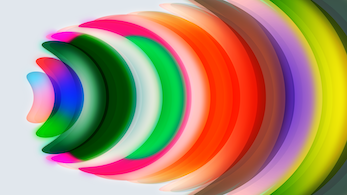
Pricing
Custom pricing options
How can we make this page better?
Legal
Content disclaimer
Support
Vendor support
We are committed to providing exceptional customer service. We provide regular updates and reports to our customers to ensure that they are aware of the progress of their Factory Modernisation Assessment and the recommendations that have been made. We welcome all feedback from customers, either direct to your Clevvi representative or via our website <www.clevvi.com.au >.