AWS for Industries
How to build a smart production solution with DXC’s SPARK platform – Part 2
This blog is the second in a two-part series on how DXC Technology, an Amazon Web Services (AWS) Partner, is building solution accelerators and a flexible platform using AWS products to expedite production and improve distribution in consumer packaged goods (CPG) companies. If you haven’t read part one, please reference the material here.
In part one of this series, we introduced you to DXC’s SPARK platform, a flexible platform and service designed to accelerate production and distribution improvements for CPG customers.
In this blog, we’re building on the challenges and key functional areas of the platform’s five solution accelerators discussed in part one and diving deeper into industry manufacturing challenges, benefits of respective solution accelerators, solutions’ feature sets, and high-level reference architecture of each solution accelerator built on DXC’s SPARK platform.
Production visibility solution accelerator
The production visibility solution accelerator helps monitor and report on production status against your production schedule, collects diversion reasons, and reports on downtime.
Challenges this solution addresses | Solution benefits |
|
|
What does the production visibility solution accelerator feature?
1.Real-time visibility of production line
The production visibility solution accelerator provides near-real-time visibility for operators to see the status of their machines and the process against the planned production rates, as well as the condition (typically imported from the enterprise resource planning system) for availability and performance or the conditions of your choice.
The solution uses a set of edge and cloud Internet of Things (IoT) services to collect data, an analytics service to analyze the production condition, an alerting and task management system, and a prebuilt user interface.
![]() |
Machine is producing against the plan |
![]() |
Machine isn’t producing against the plan and is nonoperational due to issues—outer square amber/red |
![]() |
Machine isn’t producing against the plan due to performance issues—inner square amber/red |
2. Issue details
The dashboard provides a list of all machines running outside of target conditions with details on location and other attributes.
3. Task assignment and status
Tasks are provided in a simple task list with rules showing which tasks are not started, which are overdue, and which are complete. They are assigned to operators when machines require attention and can range from entering a diversion to loading or unloading material and performing quality or safety checks.
4. Diversion reason intake
Diversion capture tasks are shown in this visual with reasons the operators can choose. Reason types can be customized.
5. Diversion reporting
The extensive reporting dashboard can detail different aspects of diversion, such as:
- Reason for the diversion (why machine was not performing)
- How long machines were not performing
- Machine with the highest number of diversions
- Shift/times of day with the highest number of diversions
Reference architecture
Quality control solution accelerator
The quality control solution accelerator helps detect product defects during production, raising alerts in near-real-time when detected, and provides defect reporting to improve quality control processes.
This solution uses a combination of edge and cloud services to capture images of the products. It also uses computer vision with trained models, an alerting and task management system, and a prebuilt user interface.
Challenges this solution addresses | Solution benefits |
|
|
What does the quality control solution accelerator feature?
1. Real-time dashboard
A real-time dashboard identifies and raises alerts when it detects a defect. It raises alerts when it detects a product anomaly; it then raises a task and assigns it to the appropriate resource for attention.
2. Human-in-loop capability
In the quality control solution accelerator, defective products are displayed on the interface and navigated either from the tasks or the navigation menu. The assigned production line user is then requested to evaluate the detected product defect and enter the action taken on the production line if the defect detection was accepted.
Reference architecture
The solution uses a technology called computer vision which uses machine learning (ML) capabilities to automate detection in real-time of defects in products within a production line or a particular work cell.
Predictive maintenance solution accelerator
The predictive maintenance solution helps monitor machine health status and predict failures across various conditions.
This solution uses:
- A combination of edge and cloud IoT services to collect data
- An ML service to establish a machine’s healthy baseline
- An analytics service that monitors that baseline
- An alerting system for when the baseline deviates
- A reporting service to see current and historic machine health
Challenges this solution addresses | Solution benefits |
|
|
What does the predictive maintenance solution accelerator feature?
1. Real-time dashboard
Start monitoring your equipment in minutes with automatic and advanced analysis through the Amazon Monitron end-to-end system, which reduces unplanned equipment downtime with predictive maintenance and machine learning.
2. Prediction using historical data
The predictive maintenance solution accelerator detects machine issues before they occur with ML and then acts. It also improves system accuracy nearly continuously as Amazon Monitron learns from technician feedback entered in the mobile and web apps.
Reference architecture
The solution is built using the Amazon Monitron service. Amazon Monitron is a complete system that uses ML to detect abnormal conditions in industrial equipment.
Environmental impact solution accelerator
The environmental impact solution accelerator is capable of capturing energy usage across factories, analyzing and visualizing the data in real-time and producing reports to help organizations improve their energy consumption. It combines the energy usage data with other data sources, such as cost, machine condition, and scheduling data. This provides enriched information to show energy usage produced by each product, as well as each individual machine condition, and relate it to the cost of production.
The solution uses smart sensors (electrical, gas, water), a combination of edge and cloud IoT services, integration services, analytics services, and a prebuilt user interface.
Challenges this solution addresses | Solution benefits |
|
|
What does the environmental impact solution accelerator feature?
Using real-time dashboarding, the environmental impact solution accelerator improves energy usage visibility. Below is an example of an energy usage report.
Reference architecture
Operational intelligence solution accelerator
The operational intelligence solution accelerator tracks key performance indicators and improves decision-making in production and distribution.
The solution uses integration services to collect data from multiple sources, analytics services to combine and analyze the data, and reporting services to visualize the information.
Challenges this solution addresses | Solution benefits |
|
|
What does the operational intelligence solution accelerator feature?
The operational intelligence solution accelerator features dashboards for decision-makers to get intelligent insight from the captured data. Below is an example of a business intelligence dashboard.
Reference architecture
Safety and Compliance
The Safety and Compliance Accelerator uses computer vision technology to enhance safety and compliance standards on the manufacturing floor. It can be used to ensure that employees are appropriately positioned in the correct locations. It can also verify if employees are equipped with the necessary personal protective equipment such as a hard hat or a face mask.
The solution accepts input from edge devices, such as industrial cameras, and performs inference using models deployed on AWS IoT Greengrass, an open source IoT edge runtime and cloud services that helps companies build, deploy, and manage IoT applications on their devices. It utilizes AWS IoT Core as a control service to facilitate secure two-way communication between edge and cloud services. For analytics, the solution employs AWS IoT SiteWise, Amazon Athena, and Amazon QuickSight. The models are trained using Amazon SageMaker in the AWS Cloud.
Challenges this solution addresses | Solution benefits |
Production downtime caused by the absence of a worker from a critical location | Alerts are triggered whenever key personnel are absent from the production line, which allows for remedial actions to be taken to prevent productivity losses |
Lack of proactive measures to prevent safety incidents on the manufacturing floor | Alerts are triggered when the system identifies a lack of established safety standards. This could be the absence of personal protective equipment, such as hard hats, on personnel, or the lack of protective equipment on the manufacturing floors, such as barriers. |
Start SPARK-ing change in your organization
Need to make production or distribution improvements? The DXC SPARK platform on AWS can help you accelerate time to achieve both, helping you modernize your production operations with lower costs and greater speed to improvement.
To request a demo, visit DXC Technology or contact your AWS account team today to get started.
Learn more about DXC SPARK consulting offers:
- Production Visibility Consulting Offer – DXC CPG IoT Production Visibility solutions help to monitor production health against your schedule.
- Predictive Maintenance Consulting Offer – DXC CPG IoT Predictive Maintenance solution helps to monitor machine health status across various conditions.
- Quality Control Consulting Offer – DXC CPG IoT Quality Control solutions help to detect product anomalies during the production phase.
- Environmental Impact Consulting Offer – DXC CPG IoT Environmental Impact solution helps to capture, analyze, and monitor energy usage data in real time.
- Operational Intelligence (OI) Consulting Offer – DXC CPG IoT OI solution helps to track metrics and improve decision-making in production and distribution.
AWS Partner spotlight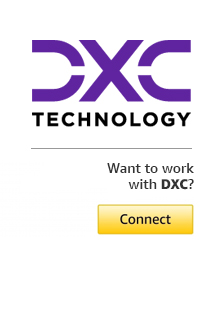
With over 10,000 AWS-accredited professionals, DXC helps enterprises incorporate smart production into their processes through connected machinery, computer vision, connected worker, operational intelligence, and power monitoring solutions. The DXC SPARK platform’s AWS-native architecture provides out-of-the-box architectural patterns, reliability, scalability, and integration with powerful AWS analytics tools.