AWS Smart Business Blog
Revolutionize Small and Medium Business Retail Operations with Digital Supply Chain Management
For many, the health of one’s business depends on the health of its supply chain. We often hear from small and medium businesses (SMBs) that their supply chains face challenges such as demand planning, forecasting and a widening supply chain talent gap. This leaves them exposed to challenges that larger enterprises can more easily address through the sheer size of their companies. But regardless of staffing and other important resources, Gartner, found more than 70 percent of leaders say their supply chains are facing greater and more frequent disruptions.
However, all is not lost, because you can reinvent your supply chain and address these challenges to become a smart business. This blog post will explore the challenges SMBs face and explain how to use existing solutions and tools to build a more resilient supply chain with greater visibility in the cloud.
What are the supply chain challenges SMBs face?
SMBs typically have limited resources when it comes to purchasing power, building supplier relationships, and adopting technology. We recognize you’re constrained in areas venture capital-funded startups and publicly-traded enterprises are not. This could result in:
- Longer delivery times
- Inventory shortages
- Reduced revenue
- Smaller margins
Retail Week discovered a quarter of supply chain and IT leaders do not feel their senior team understand the difficulties they face. Read the key challenges that typical SMBs face with their supply chain management:
Connecting all data sources
Data is frequently segregated across business divisions, functions, and technology stacks, limiting a cohesive and holistic view of operations. One issue is the inability to provide real-time data for analysis, hampering their ability to make quick and data-driven decisions. Compounding this problem, is the high development backlog and the absence of dedicated technology teams, that many SMBs contend with, making it difficult to implement much-needed improvements swiftly. Moreover, a lack of connectivity to external data sources, like shippers or environmental data, leaves them disconnected from critical insights.
Intelligent process automation
A lack of continuous monitoring leaves SMBs vulnerable to inefficiencies and potential disruptions that could have been avoided. High-volume, low-value tasks could require time from the few staff members you have and divert away from critical initiatives. Tasks such as reporting, resource planning, and monitoring can be re-allocated to smart services or software so your human staff can focus on strategic efforts that help your business grow.
Operations execution
Inefficient machine use can significantly hinder productivity, often leading to high machine downtime that consumes important operational hours. The consequences extend to logistics, where non-optimized end-to-end routing results in skyrocketing prices.
When labor costs exceed the operational budget, it can put a burden on resources and inhibit growth. In addition, maintaining inventory balance and agility in reaction to market fluctuations is a constant struggle. The absence of visibility across the entire business can create silos that hinder collaboration and decision-making.
Supply chain visibility
The inability to quickly respond to recalls not only jeopardizes customer safety, but may also cause significant damage to your brand’s reputation. Similarly, the struggle to adapt to changing government regulations can result in compliance issues and legal complications. When there is a lack of traceability and transparency, collaborating with partners becomes difficult.
Without the ability to engage in “what if” scenario planning, businesses lack a proactive approach for minimizing risks. Low customer loyalty or retention rates exacerbate these concerns, emphasizing the importance of firms addressing these issues. Solutions could support adaptation, compliance, and customer trust in a rapidly moving industry.
Product lifecycle
A failure to capture appropriate demand signals can result in out-of-stock items and dissatisfied customers. A low level of on-time-in-full (OTIF) orders can erode trust and impact revenue. The inability to adjust prices based on component costs can affect profitability and competitiveness. Real-time allocation of inventory to specific customers and rapid response to fluctuating demand are critical, yet these capabilities are often lacking for SMBs. Unreliable forecasts with high error margins can disrupt supply chain planning and decision-making.
SMBs should confront these challenges head-on, seeking innovative solutions that enhance demand visibility, optimize inventory management, and improve forecasting accuracy to thrive in today’s dynamic market.
Benefits of moving your SMB’s supply chain to the cloud
SMBs tend to be very nimble and respond quickly to market changes, so they need systems that are flexible, and easy to configure and change. With cloud services from Amazon Web Services, you can build a supply chain that relies on autonomy and monitoring. It helps SMBs apply machine learning to processes such as demand planning and forecasting.
Here are a few ways SMBs can use the power of cloud technology to build smart supply chains:
Operations and automation
SMBs such as yours are looking to reduce fulfillment costs, improve labor productivity and inventory accuracy, reduce their out-of-stocks and increase their revenue. The below categories can help you achieve your business objectives:
Warehouse management
Warehouse managers are the glue that hold together your business operations. They need tools to improve labor productivity, track inventory accurately, and visualize the space in real time. If you have aspirations to integrate robotics or other smart devices and automate physical operations, this is a smart step forward.
Predictive maintenance for vehicles
No in-house IT staff? No problem. SMBs can leverage existing AWS Partner Network solutions to accurately predict maintenance for their fleet and reduce the time spent in unplanned vehicle failures. These existing solutions take in multiple data points using sensors on the vehicles, tire degradation, and more to help you identify problems before they occur.
Order fulfilment and distribution
Distribution networks can get overly complex. SMBs looking to improve OTIF metrics, reduce their costs and also attribute and analyze Environmental, Social, and Governance-related (ESG) metrics associated with their operations can work with AWS Partners for order fulfillment and distribution solutions.
Order Fulfillment and Distribution solutions support multi-channel fulfillment and visibility into global inventory. This helps improve OTIF metrics, reduce fulfillment costs, and address ESG metrics. If you’re in the European Union, read more about the regulations for SMBs.
Planning and optimization
SMBs can use the range of AI services which provide them the benefit of not having to hire large teams to build and deploy their own models as they can leverage existing ones. You can use some of our ready-to-use AI solutions specifically for SMBs. For example, Minfy, is part AWS Partner Network and can help you forecast business demand. This is ideal for SMBs who have no in-house IT staff.
SMBs which have engineering or analytics teams however can easily create, deploy and manage their own ML models on Amazon SageMaker where they can take advantage of fully-managed infrastructure tools and workflows.
Improving forecast accuracy
SMBs can get more accurate time-series forecasts by using solutions such as Amazon Forecast. You can combine your own historical sales data, or inventory with any other data that relates to your operations such as descriptions of your products, external events like holidays. Amazon Forecast can then inspect this data, select the most appropriate algorithm for forecasting, and then train a custom model. You can then generate forecasts on your inventory levels or demand as an example.
SMBs can also improve capacity optimization by integrating more accurate forecasting into existing business processes. Using AWS Supply Chain you can easily connect data across systems, unify your data into one place, and get actionable AI-powered insights. You can empower demand planners to collaborate across teams to help avoid excess inventory costs and waste. With AWS Supply Chain Demand Planning, you can also get real-time forecast updates allowing you to proactively adjust supply chain operations.
Improving your planning capabilities
Integrated business planning is another avenue your smart business may wish to explore by using off-the-shelf offerings built by AWS Partner Network consultants. These solutions take into account different metrics such as sale orders, promotions, inventory, and sourcing to allocate your resources in the best way while also keeping an eye into the risk factor of changing demand and available supply.
Visibility and control
Around 70 percent of supply chain leaders say their supply chain is facing greater and more frequent disruptions, according to Gartner making the need for end-to-end supply chain visibility more critical to increase operational efficiency, reduce costs, and improve customer satisfaction.
You can use cloud solutions such as AWS IoT services paired with ML learning capabilities to get more visibility across many different supply chain areas such as last mile, middle mile, inventory, and logistics, but also accurately track your assets and optimize your supply chain network.
You can also use inventory and logistics solutions such as AWS Supply Chain or AWS Partner Network offerings to bring together all siloed data. It can help show you end-to-end supply chain visibility and make informed decisions.
Cando Rail Services, is an AWS SMB customer based in the US which provides specialized services to railways and industrial customers across North America. Cando developed Quasar, a platform which provides a way for rail companies to optimize their supply chains by giving them real-time visibility on their railcars and it eliminated the need for manual tracking. Cando and their AWS Partner Network consultant, Onica by Rackspace, lowered operational costs which is always critically important for SMBs.
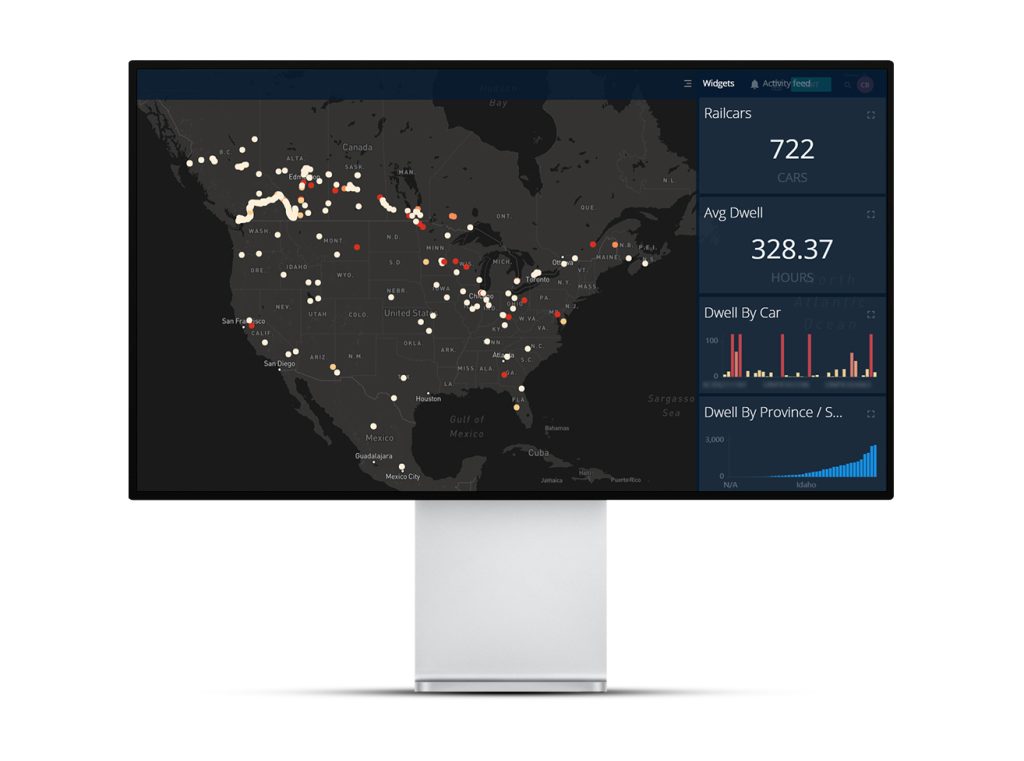
Cando recently developed Quasar, a platform for supply chain optimization that is powered by the Internet of Things (IoT) and runs on Amazon Web Services (AWS).
Next steps
As SMBs navigate the complex landscape of modern supply chain management, embracing cloud solutions is not just a choice; it’s a necessity. By harnessing the power of digitization and automation, through cloud services on AWS, SMBs can transform their supply chains, adapt to change, and thrive in today’s dynamic market. The journey of supply chain excellence begins with the strategic adoption of cloud solutions.