AWS for Industries
IDEMIA: How a global leader in identity leverages AWS to improve productivity in Manufacturing
Introduction
When you travel abroad, your passport may have been manufactured by IDEMIA, or when you pay with bank cards, which may also come from IDEMIA. Spanning over 40 industrial sites worldwide, IDEMIA produces highly confidential products such as bank cards, passports, and SIM cards, totaling over 800 million bank cards a year. IDEMIA is a multinational technology company that provides identity-related security services, both physical and digital.
In manufacturing, most companies, like IDEMIA, strive to improve the OEE (Overall Equipment Effectiveness) of their industrial equipment to provide their customers with lower costs, on-time deliveries, and better quality. In 2022, IDEMIA initiated a global program to enhance productivity focused on Industry 4.0 in their industrial sites. In less than six months, IDEMIA successfully deployed two use cases in one of its major factories located in Shenzhen, China.
These two use cases reduced the downtime of Cobots (collaborative robots) by up to 10% and extended the Cobots’ lifespan by two years – which is typically 12 to 15 years. IDEMIA’s Chief Data Officer shares details in this interview video (in French).
IDEMIA’s challenges & strategy
1. How to initiate business impact in Industry 4.0
Getting stuck in the proof-of-concept (PoC) purgatory is the top risk more than 40% of customers (Source: LNS Research, 2020) for Industry 4.0 programs. Many companies tend to build a holistic strategy by benchmarking all available solutions in the market and spending years building a platform as a foundation. Even though establishing strong foundations (connectivity, security, data platform, governance, etc.) at the very beginning is important, this approach requires substantial capital expenditure (CAPEX) and presents significant risks to IDEMIA, given the uncertainty of return on investment (ROI) and changes in market conditions over such a long time period.
IDEMIA prioritized and clarified a rollout plan for the industrial use cases they listed, aligned with budget frugality. They adopted an agile approach and an industrial value flywheel (or virtuous cycle), as shown in the diagram below.
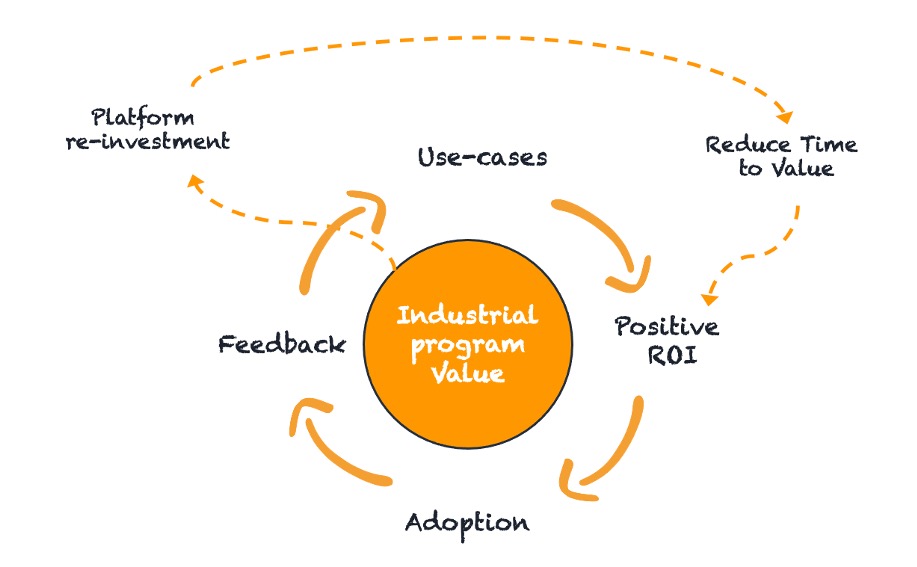
Figure 1. Industrial value Flywheel
At IDEMIA, the flywheel started by prioritizing and grouping high-value and low-hanging use cases that could be implemented quickly and easily. The Cobot use cases were selected because they provided a clear business impact and had low technical complexity. Deploying these use cases in production generated a positive ROI in a short period of time for IDEMIA. It not only increased the profitability and efficiency of the industrial sites but also created a positive feedback loop that fostered further adoptions and investments. With the benefits generated from this initial use case, IDEMIA had the opportunity to reinvest in the IoT platform, making it more robust and scalable. This mitigated risks, lowered costs for the next use cases, and improved the performance and reliability of the existing ones. Demonstrating tangible benefits of Industrial Internet of Things (IIoT) solutions expanded adoption and engagement across IDEMIA’s organization, fostering a culture of continuous improvement and learning.
2) Aligning OT and IT silos
Another challenge for manufacturing organizations is bridging the gap between operational technology (OT, i.e., industrial automation) and information technology (IT). These functions often have different goals, cultures, processes, and systems, which can create barriers to collaboration and innovation.
To overcome this challenge, IDEMIA adopted a single-threaded approach that integrated both OT and IT teams at the start of the project. This approach is a way to unite teams around a specific goal. The cross-functional team, comprised of both OT and IT experts, streamlined communication and coordination throughout the project lifecycle. The team worked together daily on use case prioritization, dashboard designs, requirements analysis, sensor and IoT gateway setup, and solution deployment. By doing so, they improved their understanding, skills, knowledge, environment, and tools. This approach enabled the faster and smoother delivery of industry 4.0 solutions, meeting the needs and expectations of both OT and IT stakeholders.
3) How AWS Prototyping Team accelerates the adoption
Building a manufacturing solution is challenging because it involves not only IoT services at the edge to connect to different machines, but also data transformation pipelines and analytics programs in the cloud to generate insights. This end-to-end solution requires a multi-competency team that most companies still need to develop internally.
AWS prototyping teams can help customers accelerate their decisions. They enable their developers to build new workloads on AWS through hands-on experimentation. For IDEMIA, they worked jointly in a time-boxed engagement (6 weeks) and built the first iteration of the solution. They delivered assets and enabled IDEMIA developers with skills, best practices, and confidence to continue with subsequent workloads from prototype to production.
IDEMIA Cobot optimization use cases
Cobots are collaborative robots that work alongside human operators on the shopfloor. They are used to move unfinished stacks of cards from one process to another. However, Cobots are sensitive to external and unexpected events. They may stop due to mechanical noises. This can cause a significant loss of production and hours of work for engineers.
IDEMIA used non-intrusive IFM sensors attached to the Cobots to retrieve vibration metrics. These metrics indicate the impact and fatigue of the Cobots, and can identify the root cause of abnormal stops. IDEMIA leveraged AWS IoT services to collect, process, and visualize sensor data in near real-time.
The shop floor engineers and the project team designed a dashboard and displayed the actual status of a Cobot. On the right side, there is a picture showing the Cobot’s environment, which helps the field engineer quickly locate the Cobot. On the left side, there are two status indicators about the Cobot: 1) ON/OFF: working state of the Cobot; 2) Status: normal or abnormal. A Cobot can be “off” and “normal” when it has a complete, correct cycle, or it can be “off” and “abnormal” when the cycle is not done and abnormal vibrations are detected.
On this dashboard, the engineers can monitor the Cobots remotely and reduce the downtime by up to 10%. This predictive maintenance also improves the Cobot’s lifespan by two additional years.
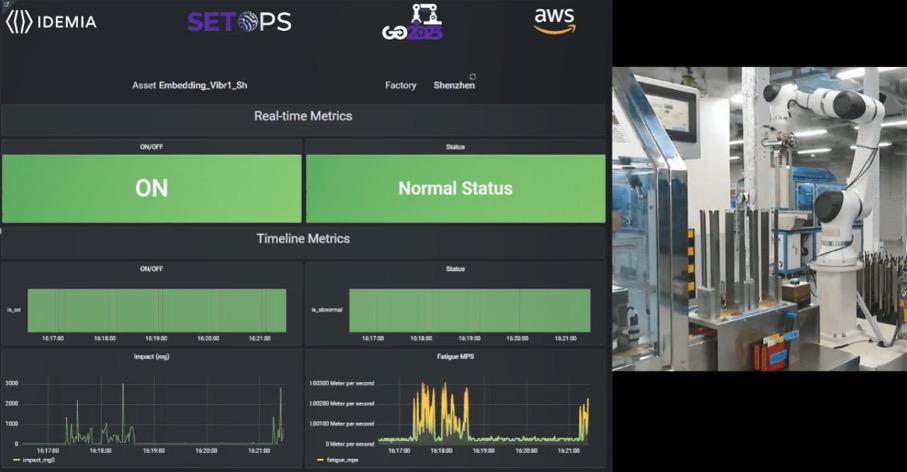
Figure 2. Dashboard for Cobot monitoring
The factory manager can access another dashboard, which compiles an overview of the status of Cobots related to different production lines. An “Overview” section displays the total number of devices, with the percentage of devices labeled “ON” and “Abnormal”. Managers can quickly identify any issues with the production process.
The “Devices Status” section shows the historical data of each device, such as normal and abnormal stops. The engineers can use this section to explore the timeline and gain a deeper understanding of the performance and behaviors of each Cobot. They can then optimize the Cobot’s path generation and allocation.
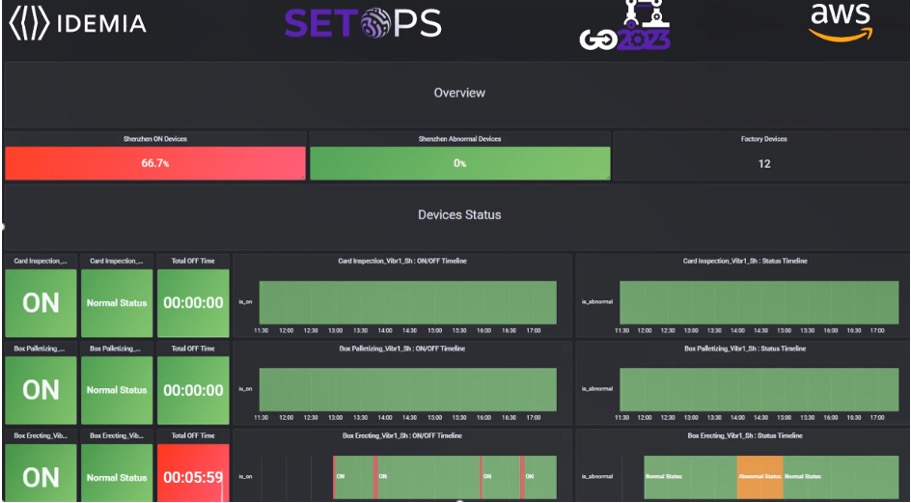
Figure 3. Dashboard for Factory monitoring
Operation executives can access to a global dashboard about devices status. The dashboard displays the number and percentage of devices “ON”, “OFF”, “Normal”, and “Abnormal” in each factory. The executives can compare the performance and productivity of different factories and identify any gaps or opportunities for continuous improvement.
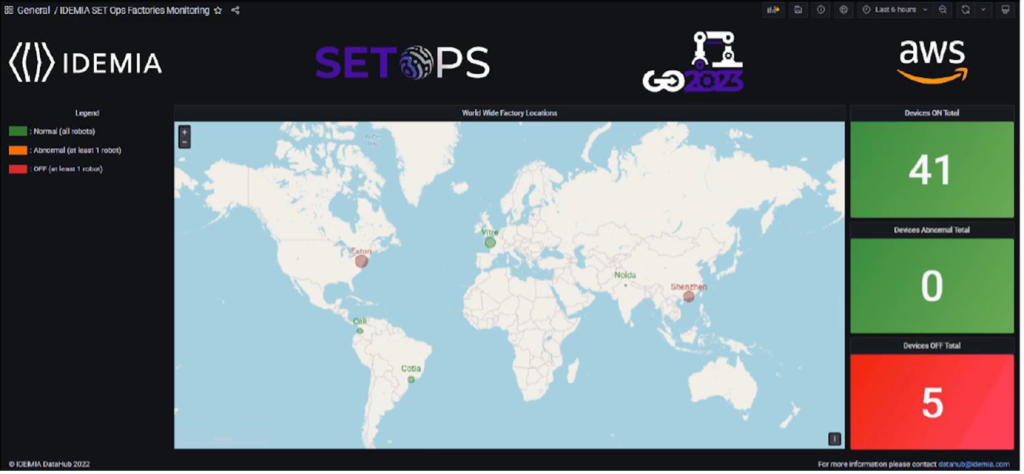
Figure 4. Global dashboard for Executives
Backend architecture
The following diagram displays the high-level architecture with associated AWS services.
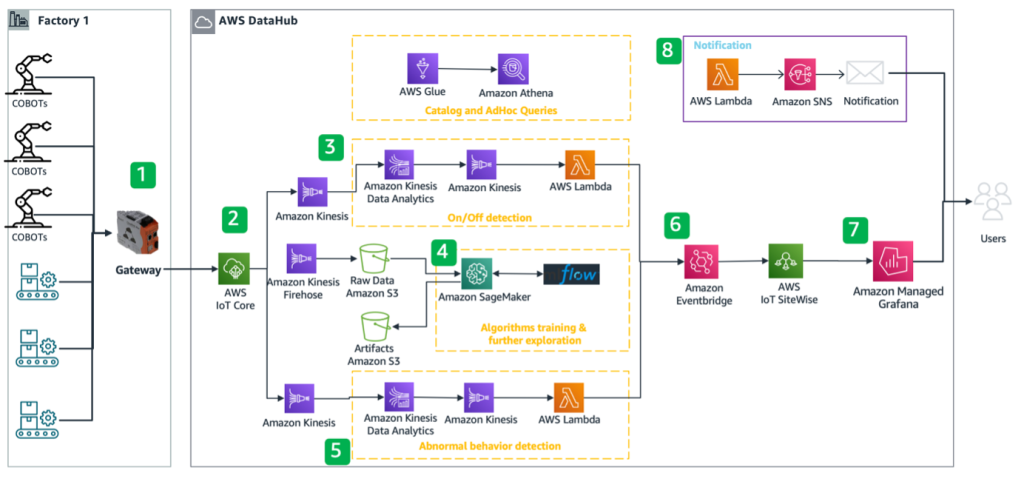
Figure 5. High-level IIoT architecture
Industrial data capture and global sharing
The first step in the flow of the architecture is to collect locally and share globally the industrial data from the shopfloor. An industrial edge gateway connects to IFM sensors through the IO-Link protocol and sends the sensor raw data to AWS IoT Core (see block “1” in Figure 5). AWS IoT Core serves as a central entry point for raw data generated by IoT devices in the field, making it readily available for processing by various downstream services.
One of the downstream services is Amazon Kinesis Data Streams, which collects data from AWS IoT Core based on IoT rules and enables data analytics for different use cases, such as “On-Off” and “Abnormal behavior” detection (see block “2” in Figure 5).
Another downstream service is Amazon Kinesis Firehose, which ingests raw data from AWS IoT Core into Amazon S3 (see block “3” in Figure 5). Amazon S3 is the central storage for the Datahub, which allows data engineers to run ad-hoc queries through Amazon Athena (see block “4” in Figure 5). It also allows data scientists to create machine learning models with Amazon SageMaker (see block “5” in Figure 5).
All analytical results are streamed to a single service, Amazon EventBridge (see block “6” in Figure 5), which allows new data consumers or publishers to immediately and easily integrate and use data. This also makes the architecture modular and expandable. The approach initiates an industrial IoT platform that can support other use cases later on.
Machine learning with Amazon SageMaker
IDEMIA leverages advanced machine learning models for inspection by detecting whether the Cobot is “ON“ or “OFF” using the vibration data (see block “4” in Figure 5). Models are trained with historical machine data collected through the Amazon Kinesis Firehose and stored in an S3 bucket.
Near real-time On/Off detection
To analyze the Cobot’s “ON” and “OFF” status, real-time streaming data was aggregated over a given interval and sent to Kinesis Data Stream, which triggered an AWS Lambda function. This function uses a model stored in Amazon S3 to infer and send results to Amazon EventBridge.
Near real-time abnormal behavior detection
The approach was similar to the “ON/OFF” detection, but the model uses different metrics to detect abnormal vibration. The inference results were also sent to EventBridge.
Device status dashboards
AWS IoT SiteWise is used as a central industrial asset and data management service. It aggregates and parses data between hierarchies, for instance, by aggregating the number of abnormal sensors in a plant. Amazon Managed Grafana (see block “7”) uses AWS IoT SiteWise as a data source to create the dashboards mentioned in the previous section. IDEMIA uses AWS SSO to allow their employees to access the Grafana dashboards.
Notifications
An AWS Lambda function is defined to implement the business logic (e.g., Cobot is abnormal for x-minutes) and uses Amazon Simple Notification Service to send notifications towards the industrial staff (see block “8” in Figure 5) for timely actions.
Conclusion
IDEMIA has been leveraging AWS to improve productivity with manufacturing solutions, and they are already seeing results. IDEMIA adopted a flywheel approach to start small, think big, and scale fast. They leveraged AWS Prototyping Teams to innovate quickly and learn new skills through pragmatic use cases. They also built a global industrial IoT platform that can support future use cases.
For other details on how AWS and partners can accelerate the industrial digital transformation of our customers, please check the AWS for industrial website.